| | | | | | | |
Configuration Components: Process connectionsThis catalog is limited to the standard versions. Special versions are available on request. The technical data are provided to assist the user. It is the responsibility of the ordering party to make the correct selection of suitable devices. Welding in The welding in of the protective tube provides a permanent, secure and highly resilient process connection, assuming a respective welding quality. It is not possible to accidentally open the process connection. Additional gaskets are not required. If the pipeline is not thick enough to ensure a secure welded joint, appropriate weld-in sockets are used. With weld-in sockets in suitable length, it is also possible to standardize a plant's measuring points to a large extent. Stocks of spare parts can therefore be reduced to a minimum.  Weld-in sockets Thread Type of installation: Screwed plug Screwed plugs of different thread types and sizes are firmly welded to the protective tube  Screwed plug Type of installation: Compression fittings Compression fittings are available as accessories. They fit the diameter of the protective tube and provide for flexible installation. The installation length can be selected on site. When installed correctly, compression fittings are well suited for low and medium pressure. The difference between the standard and spring-loaded version is as follows: In the case of the spring-loaded compression fitting, the sensor is pressed against the measured object or the base of the protective tube, thus achieving particularly good heat contact.  Compression fitting  Spring-loaded compression fitting Thread form: Cylindrical thread Cylindrical threads do not seal in the thread but due to an additional sealing face or seal. For example, threads with the short form "G" (as per ISO 228) feature a thread form with a defined screw gauge.  Cylindrical thread Tapered thread By contrast, tapered threads, such as the American "NPT" thread, seal metallically in the thread. The relevant length information in the catalog refers to the "fully-tightened point (hand-tight)" of the thread, which cannot be defined exactly due to standard-related tolerances. However, the spring-load of the measuring insert compensates for the differences in length.  NPT thread | Thread form: | E / E1 | K1 | K1 |
---|
Protective tube shape 2G + 3G | Cylindrical | G 1/2" | 15 | 27 | G 1" | 30 | 46 | Tapered | NPT 1/2" | 9 | 30 | Extensions 7MC7500 | Cylindrical | M14 x 1.5 | 12 | 23 | M18 x 1.5 | 12 | 25 | G 1/2" | 12 | 27 | Tapered | NPT 1/2" | 9 | 33 |
X = extension length U = installation length E1 = neck tube / process connection K1 = penetration depth K2 = length of the process connection Flanges The different properties of the flanges are as follows: - Standard series EN 1092, ASME 16.5,..
- Nominal pressure
- Nominal diameter
- Sealing face
This information is also stamped into the flange, along with the material code and batch number for "3.1 Material". Industry-specific process connections Special process connections have become popular in different industries. For example, hygiene technology: clamp-on connections, dairy connections and others. Components: Protective tubeProtective tubes or protective sleeves fulfill two basic functions: - they protect the measuring insert from aggressive media
- They make it possible to replace units during ongoing operation
This catalog is limited to the standard versions. Special versions are available on request. The large number of available types can be classified as follows: - Protective tubes made of tube material
Protective tubes made of tube material are also described as "welded" or "multi-part" protective tubes (not to be confused with "multi-part protective fittings"). They are suitable for low to medium process loads and can be manufactured on a cost-effective basis. Versions:- Form 2N similar to DIN 43772
with straight tip and shortest possible extension length non-alignable connection head - Form 2 as per DIN 43772
with straight tip and extension alignable connection head Form 2: without process connection Form 2G: Threaded connection Form 2F: Flange connection - Form 3 as per DIN 43772
Version with tapered tip and extension alignable connection head For these protective tubes, the protective tube tip is tapered by rotary swaging. This results in an excellent fit with the measuring insert and very good response times. Analogous to forms 2, versions 3G/3F are also available for form 3
- Protective tubes made of barstock according to DIN 43772
Where process loads are too great, or where a protective tube cannot have a welded seam, deep-hole drilled protective sleeves made of barstock are used. Protective tubes of form 4 as per DIN 43772 are frequently used. Forms D1-D5 of the previous standard DIN 43763 have been integrated into form 4 of DIN 43772:
Design DIN 43763 invalid | Design 4 DIN 43772 current |
---|
| L in mm | U in mm | D1 | 140 | 65 | D2 | 200 | 125 | D4 | 200 | 65 | D5 | 260 | 125 |
The following table shows the dimensions of the different protective tubes. | Tip | Process connection |
---|
∅ Inner [mm (inch)] | ∅ Outer [mm (inch)] | ∅ Inner [mm (inch)] | ∅ Outer [mm (inch)] | Protective tube type, version | D1 | D2 | D3 | D4 | 2N/2/2G/2F, tube | 7 (0.28) | 9 (0.35) | 7 (0.28) | 9 (0.35) | 2/2G/2F, tube | 7 (0.28) | 12 (0.47) | 7 (0.28) | 12 (0.47) | 3/3G/3F, tube | 6 (0.24) Tolerances as per DIN 43772 | 9 (0.35) | 7 (0.28) | 12 (0.47) | 4/4F, barstock | 7 (0.28) | 12.5 (0.49) | 7 (0.28) | 24 (0.94) | 4/4F, quick-response, barstock | 3.5 (0.14) | 9 (0.35) | 3.5 (0.14) | 18 (0.71) |
 Sizing of protective tubes Protective tubes made of barstock according to ASME B40.9Protective tubes according to ASME are distinguished by their form: Straight, reduced (staggered) or tapered along the entire installation length. Coarse subdivisions can also be made in the type of process connection: for screwing in, for welding, with flange or with the so-called Van Stone connection. For the Van Stone connection, a small flange sealing surface exists directly at the protective tube in barstock. This prevents any welding seams in the area touching the media. The protective tube is fixed by a collar flange that presses the sealing surface against the plant-side flange. Another advantage of this design is the optimized spare parts inventory. A protective tube fits onto multiple connecting flanges; the only difference is in the collar flanges. Components: Extension (neck tube)The extension is the section from the lower edge of the connection head to the fixed point of the process connection or protective tube. There are a variety of terms for this component, e.g. neck tube. For this reason the term extension has been selected as a standardized term for the different designs. Function is the deciding factor: - Thermal decoupling of connection head from process temperature
- Installation of connection head over existing insulation
- Simple standardization of measuring inserts: In general, the length of the extension may be freely selected. However, when using standardized installation lengths, the option "Extension as per DIN 43772" is recommended. This ensures that measuring inserts which are quickly available can be used. In the case of special lengths, it is possible to standardize the measuring insert length through a clever combination with the respective special extension length. This allows customers to optimize their costs in purchasing and logistics.
- For American-type sensors, the extension also undertakes the spring load of the measuring insert.
- Depending on the version, the extension can also enable the alignment of the connection head
- The form of the extension depends on the form of the protective tube:
- Protective tube made of tube material
The extension and protective tube usually consist of one continuous tube. The process connection is welded on (= one-piece protective fitting). - Protective tubes made of barstock
Extension and protective tube consist of two components which are welded together. The process connection is attached to the protective tube (= multi-piece protective fitting).
Protective tube type | X [mm (inch)] | M [mm (inch)] | Divisible |
---|
2G | 129 (5.08) | 145 (5.71) | No | 2F | 64 (2.52) | 80 (3.15) | No | 3G | 131 (5.19) | 147 (5.79) | No | 3F | 66 (2.60) | 82 (3.23) | No | 4 (only L=110) | 139 (5.47) | 155 (6.10) | Yes | 4 (others) | 149 (5.87) | 165 (6.50) | Yes |
 Extensions as per DIN 43772 Versions With regard to their function, extensions can be classified into two types: - Alignable/non-alignable:
Function of the extension to align the connection head to the desired direction - Integrated measuring insert spring load:
In the case of American-type sensors, the spring load of the measuring insert is integrated into the extension. Measuring insert and extension form one unit.
European type Alignable, cylindrical | European type Alignable, tapered | Without extension Without thread (optional sealing screw) |  |  |  | European type Non-alignable, cylindrical | European type Non-alignable, tapered | European type Non-alignable, Nipple (NIP) |  |  |  | European type Alignable Nipple-Union-Nipple (NUN) | American type Alignable Nipple-Union-Nipple (NUN) | American type Non-alignable, Nipple (NIP) |  |  |  |
Versions; in the case of heavy stainless steel connection heads in conjunction with vibrations, a short extension length should be chosen or external support should be provided. Components: Connection headConnection head the connection head protects the connection department. The connection head features sufficient room for mounting a clamping base or transmitter. Different connection heads are used depending on the application and preference. Connection head | Type Material | Designation | Cable gland | Degree of protection | Transmitter installation | Connection height H1 [mm (inch)] | Explosion protection optional |
---|
 | BA0 aluminum | Flange lid | M20 x 1.5 brass | IP54 | Measuring insert | 26 (1.02) | Ex i |  | BB0 aluminum | Hinged cover low | M20 x 1.5 brass | IP65 | Measuring insert | 26 (1.02) | Ex i |  | BC0 aluminum BC0 plastic | Hinged cover high | M20 x 1.5 BC0: brass BP0: polyamide | IP65 | Measuring insert and/or hinged cover | 26 (1.02) | Ex i |  | BM0 plastic | Screw cover | M20 x 1.5 polyamide | IP54, observe information in manual | Measuring insert | 26 (1.02) | Ex i |  | BS0 stainless steel | Screw cover | M12 x 1.5 polyamide | IP67 | Measuring insert | 26 (1.02) | Ex i |  | AG0 aluminum AU0 stainless steel AISI 316 (1.4401) | Screw cover, heavy-duty | M20 x 1.5 not Ex: plastic Ex i/Ex n: brass Ex d: without cable gland | IP66/68 (IP68: 1.5 m; 2 h) | Measuring insert | 41 (1.61) | Ex i, Ex d |  | AH0 aluminum AV0 stainless steel AISI 316 (1.4401) | Screw cover, window, heavy duty, with 4 ... 20 mA display | M20 x 1.5 not Ex: plastic Ex i/Ex n: brass Ex d: without cable gland | IP66/68 (IP68: 1.5 m; 2 h) | Measuring insert | 41 (1.61) | Ex i, Ex d |
Components: Measuring insert Measuring insert The measuring insert of the temperature sensor is built into the protective fitting (protective tube, extension and connection head). The sensor element is located in the measuring insert, where it is protected. The spring load of the Siemens measuring inserts provide good thermal contact with the tip of the protective tube, and vibration resistance is significantly increased. Only highly resistant mineral-insulated cables (so-called MIC or plastic-sheathed) are used for the electrical connection between the sensor element and connection head. The highly compacted insulation of magnesium oxide achieves excellent levels of vibration resistance. The following measuring insert designs are the most widely used on the world market:  |  | European type | American type |
European type European type measuring inserts can be replaced without having to dismantle the connection head. The springs are located either on the transmitter or the terminal block. This makes it possible to achieve a 8 to 10 mm spring range. If a transmitter is not attached, a ceramic base is located at this position. Order option G01 can be used to select a version with free wire ends instead of the ceramic base for mounting of head transmitters. American type American-type measuring inserts feature a large spring range. These measuring inserts are ideal for use with NPT threads that feature high tolerances. In this configuration, the extension function is partially or fully integrated (nipple-union-nipple). Moreover, it is also possible to directly attach field devices, e.g. SITRANS TF. Components: TransmittersSITRANS TH head transmitters process weak, non-linear sensor signals and transmit a stable and temperature-linear standard signal. thereby minimizing sensor signal disruptions. The transmitters permanently monitor the temperature sensors and transmit diagnostic data to superordinate systems. Because of the low energy feed of the SITRANS TH head transmitters, self-heating of the temperature sensors is at a minimal level. The electrical isolation and integrated reference junction ensure that temperature sensors with thermocouples provide reliable measurements at a low cost. SITRANS TH product family For detailed technical data on the SITRANS TH transmitters, please refer to the catalog FI 01. - TH100 - the basic device
- Output 4 ... 20 mA
- For Pt100
- Can be configured using simple software
- TH200 - the universal device
- Output 4 ... 20 mA
- Resistance thermometer, thermocouples
- Can be configured using simple software
- TH300 - HART universal
- Output 4 ... 20 mA / HART
- Resistance thermometer, thermocouples
- HART conforming
- Diagnostic functions
- TH400 - Fieldbus PA and FF
- Output PROFIBUS PA or FOUNDATION Fieldbus
- Resistance thermometer, thermocouples
- Diagnostic functions
Installation types All SITRANS-TH transmitters can be installed in type B connection heads. The following installation forms are used: - Measuring insert installation
Our standard version offers the following advantages- Small vibrating masses and compact design
- Measuring insert-transmitter unit can be replaced quickly
 Installation of measuring insert - Hinged cover installation
- Standard for head type BC0 and BP0
- Advantage: Measuring insert and transmitter can be repaired/maintained separately (recalibration).
 Hinged cover installation Measuring technology: Basic sensorsThe diverse application spectrum for industrial temperature measuring technology requires different sensor technologies. Resistance thermometer Basic sensors made of other basic materials, with different basic values or different underlying standards, are available on request. Resistance thermometers can be classified as follows: - Basic design
The sensor element is built with thin layer technology. The resistance material is applied in the form of a thin layer on a ceramic carrier material. - Versions featuring increased vibration resistance
In addition to the basic design: Measures to improve vibration resistance. - Versions with expanded measuring range
Elements in wire-wound design. The wire winding is embedded in a ceramic body.
Thermocouples Thermocouples based on other thermocouples or underlying standards are available upon request. The most common base-metal thermocouples are: - Type N (NiCrSi-NiSi) high degree of stability even in upper temperature range
- Type K (NiCr-Ni) more stable than type J, but drifts in upper range
- Type J (Fe-CuNi) narrow application band
Measuring technology: Measuring rangeThe measuring range describes the temperature limits within which the thermometer can be used in a way that is meaningful for measurement purposes. Depending on the loads present, the protective tube materials and the desired accuracy levels, among other things, the actual application range for the thermometer may be smaller. Resistance thermometer [°C (°F)] |
---|
Basic version and increased vibration resistance | -50 ... +400 (-58 ... +752) | Expanded measuring range | -196 ... +600 (-320.8 ... +1112) |
Thermocouple [°C (°F)] |
---|
Type N | -40 ... +1100 (-40 ... +2012) | Type K | -40 ... +1000 (-40 ... +1832) | Type J | -40 ... +750 (-40 ... +1382) |
Measuring technology: Measuring accuracyResistance thermometer The tolerance classes of the resistance thermometers correspond to IEC 751/EN 60751: Tolerance | Δt |
---|
Basic accuracy, Class B | ± (0.30 °C +0.0050|t[°C]|) 0.54 °F +0.0050x|t[°F]-32| | Increased accuracy, Class A | ± (0.15 °C +0.0020|t[°C]|) 0.27 °F +0.0020x|t[°F]-32| | High degree of accuracy, Class AA (1/3 B) | ± (0.10 °C +0.0017|t[°C]|) ± 0.18 °F +0.0017x|t[°F]-32| |
The following tables provide an overview of the scope of these tolerances. If the specified limits are exceeded with a resistance thermometer, the values of the next lower accuracy class apply permanently: Resistance thermometer Basic version [°C (°F)] |
---|
Tolerance | Range | Basic accuracy, Class B | -50 ... +400 (-58 ... +752)1) | Increased accuracy, Class A | -30 ... +300 (-22 ... +572) | High degree of accuracy Class AA (1/3 B) | 0 ... 150 (32 ... 302) |
Resistance thermometer Increased vibration resistance [°C (°F)] |
---|
Tolerance | Range | Basic accuracy, Class B | -50 ... +400 (-58 ... +752)1) | Increased accuracy, Class A | -30 ... +300 (-22 ... +572) | High degree of accuracy Class AA (1/3 B) | 0 ... 150 (32 ... 302) |
Resistance thermometer Expanded measuring range [°C (°F)] |
---|
Tolerance | Range | Basic accuracy, Class B | -196 ... +600 (-321 ... +1112) | Increased accuracy, Class A | -100 ... +450 (-148 ... +842) | High degree of accuracy, Class AA | -50 ... +250 (-58 ... +482) |
1) The requirements of IEC 60751 are being observed. In case of high requirements regarding long-term stability, Pt100 sensors "expanded measuring range" should be used for temperatures above 350 °C (662 °F). Thermocouples The tolerance classes of the thermocouples correspond with IEC 584/EN 60584: Catalog versions Type | Basic accuracy, Class 2 | Increased accuracy, Class 1 |
---|
N | -40 °C ... +333 °C ±2.5 °C (-40 °F ... +631 °F ±4.5 °F) 333 °C ... 1100 °C ±0.0075x|t[°C]| (631 °F ... 2012 °F ±0.0075x|t[°F]-32|) | -40 °C ... +375 °C ±1.5 °C (-40 °F ... +707 °F ±2.7 °F) 375 °C ... 1000 °C ±0.004x|t[°C]| (707 °F ... 1832 °F ±0.004x|t[°F]-32|) | K | -40 °C ... +333 °C ±2.5 °C (-40 °F ... +631 °F ±4.5 °F) 333 °C ... 1000 °C ±0.0075x|t[°C]| (631 °F ... 1832 °F ±0.0075x|t[°F]-32|) | -40 °C ... +375 °C ±1.5 °C (-40 °F ... +707 °F ±2.7 °F) 375 °C ... 1000 °C ±0.004x|t[°C]| (707 °F ... 1832 °F ±0.004x|t[°F]-32|) | J | -40 °C ... +333 °C ±2.5 °C (-40 °F ... +631 °F ±4.5 °F) 333 °C ... 750 °C ±0.0075x|t[°C]| (631 °F ... 1382 °F ±0.0075x|t[°F]-32|) | -40 °C ... +375 °C ±1.5 °C (-40 °F ... +707 °F ±2.7 °F) 375 °C ... 750 °C ±0.004x|t[°C]| (707 °F ... 1382 °F ±0.004x|t[°F]-32|) |
Other thermocouples, ignoble Type | Basic accuracy, Class 2 | Increased accuracy, Class 1 |
---|
T | -40 °C ... 133 °C ±1 °C (-40 °F ... +271 °F ±1.8 °F) 133 °C ... 350 °C ±0.0075x|t[°C]| (271 °F ... 662 °F ±0.0075x|t[°F]-32|) | -40 °C ... +125 °C ±0.5 °C (-40 °F ... +257 °F ±0.9 °F) 125 °C ... 350 °C ±0.004x|t[°C]| (257 °F ... 662 °F ±0.004x|t[°F]-32|) | E | -40 °C ... +333 °C ±2.5 °C (-40 °F ... +631 °F ±4.5 °F) 333 °C ... 900 °C ±0.0075x|t[°C]| (631 °F ... 1652 °F ±0.0075x|t[°F]-32|) | -40 °C ... +375 °C ±1.5 °C (-40 °F ... +707 °F ±2.7 °F) 375 °C ... 800 °C ±0.004x|t[°C]| (707 °F ... 1472 °F ±0.004x|t[°F]-32|) |
Other thermocouples, noble Type | Basic accuracy, Class 2 | Increased accuracy, Class 1 |
---|
R and S | 0 °C ... 600 °C ±1.5 °C (32 °F ... 1112 °F ±2.7 °F) 600 °C ... 1600 °C ±0.0025x|t[°C]| (1112 °F ... 2912 °F ±0.0025x|t[°F]-32|) | 0 °C ... 1100 °C ±1 °C (32 °F ... 2012 °F ±1.8 °F) 1100 °C ... 1600 °C ±[1 + 0.003 x(t - 1100)] °C (2012 °F ... 2912 °F ±1.8+0.003x(t[°F]-2012)) | B | 600 °C ... 1700 °C ±0.0025x|t[°C]| (1112 °F ... 3092 °F ±0.0025x|t[°F]-32|) | |
SITRANS TS300 Clamp-on Measuring accuracy | | Reference conditions | | | Pipeline 13 x 1.5 mm (0.51 x 0.06 inch) made of stainless steel using thermal paste | | 20 °C (68 °F) | | Water 120 °C (248 °F) | | 3 m/s (9.84 ft/s) | Measuring accuracy when using thermal paste (The accuracy is dependent on the geometry of the pipeline, the medium and the ambient conditions. TM = Process temperature; TA = Ambient temperature) | Process-optimized for steam sterilization | - Application, process-optimized for steam sterilization
| For 100 ... 150 °C (212 ... 302 °F) (TA-TM) x 0.01 | - Application, alternative class A as per IEC 60751
| -40 ... +150 °C (-40 ... 302 °F) (TA-TM) x 0.02 |
Measuring technology: Response timesResponse time describes the speed of the measurement system in the case of a temperature change, and is typically indicated as T0.5 or T0.9. The values indicate the time in which a measured value has increased to 50% or 90% of the actual temperature increase. The main variables which affect response time are as follows: - Protective tube geometry, ideally:
- Very little material at the tip
- use of conductive material
- Thermal connection of measuring insert to protective tube:
Because of design changes implemented for the measuring insert (small gap width, spring system), Siemens measuring inserts feature very good response behavior. Because of the good fit, additional contact materials are not usually required except in certain applications, e.g. attachment of a surface sensor. - Size of temperature increase
- Medium and flow rate
Resistance thermometer Typical values as per DIN EN 60751 in water at 0.4 m/s can be found in the following table. Protective tube form | Diameter [mm (inch)] | T0.5 | T0.9 |
---|
None | 6 (0.24) | 6 | 15 | Straight (2) | 9 (0.35) 12 (0.47) | 34 45 | 90 143 | Tapered (3) | 12 (0.47) | 15 | 31 | Barstock (4) U/C = 65 | 24 (0.95) | 40 | 100 | Barstock (4) U/C = 125 | 24 (0.95) | 40 | 110 |
Thermocouples Typical values as per DIN EN 60751 in water at 0.4 m/s can be found in the following table. Protective tube form | Diameter [mm (inch)] | T0.5 | T0.9 |
---|
None | 6 (0.24) | 2 | 4 | Straight (2) | 9 (0.35) 12 (0.47) | 20 19 | 63 66 | Tapered (3) | 12 (0.47) | 7 | 22 | Barstock (4) U/C = 65 | 24 (0.95) | 22 | 73 | Barstock (4) U/C = 125 | 24 (0.95) | 20 | 53 |
Measuring technology: Mounting depthMeasuring insert Type | Temperature-sensitive length (TSL) [mm (inch)] | Non-bendable length [mm (inch)] |
---|
Basic | 50 (1.97) | 30 (1.82) | Increased vibration resistance | 50 (1.97) | 30 (1.82) | Expanded measuring range | 50 (1.97) | 60 (2.36) | Thermocouple | 20 (0.79) | 5 (0.20) |
Immersion depth/contact with medium The "heat transfer error" arises depending on the ambient conditions (temperature/weather/insulation) and the size of the protective tube, process connection and pipeline. To prevent such an error, the submersion depth and diameter of the protective tube tip are defined. The temperature-sensitive length (TSL) of the protective tube must also be taken into account. The following rule of thumb can be used: - Water
Submersion depth ≥ TSL + 5 x Ø of protective tube - Air
Submersion depth ≥ TSL + 10 ... 15 x Ø of protective tube - Recommendations
- Select largest possible submersion depth
- Select measuring location with higher flow velocity
- Insulate outer components of thermometer
- Smallest possible surface for outer components
- Insertion in tube bends
- Direct measurement without additional protective tube if no suitable solution can be found using other measures
Measuring technology: Connection typesIn the case of resistance thermometers, the type of sensor connection directly affects the level of accuracy: Two-wire system The resistance of sensor lines are included in the measurement result as an error. Adjustments are recommended in this case.  Pt100 2-wire system Three-wire system Line resistance is not included in the measurement result. Requirements: all terminal and line resistances (corrosion) are at the same level, and terminals are at the same temperature level.  Pt100 3-wire system Four-wire system Line resistance is not included in the measurement result. This type of connection is the most secure and most accurate.  Pt100 4-wire system Siemens measuring inserts can be used to implement all types of connections for 1 x Pt100 devices. In the case of 2 x Pt100 versions, two- and three-wire systems are also possible. For measurement-related reasons, we always recommend a 1 x 4-wire or 2 x 3-wire connection. Temperature influenceAt connection head TS500 1) | Without transmitter [°C (°F)] | With transmitter [°C (°F)] |
---|
Aluminum or stainless steel | -40 ... +100 (-40 ... +212) | -40 ... +85 (-40 ... +185) | Plastic | -40 ... +85 (-40 ... +185) | -40 ... +85 (-40 ... +185) |
1) In the case of applications in hazardous areas, observe information in manual. At connection site cable/plug-in connection TS100/200 The specified measuring range applies to the hot side of the sensor. The maximum permitted temperature at the cold end depends on the cables and plugs used. <°80°C (176 °F) is considered non-critical. Influence of extension The illustration below assists you in selecting the right length for the neck tube. In this case, the following applies: Connection head temperature = Ambient temperature + Overtemperature. The temperature in the connection head can thus be assessed as follows:  Extension length X, influence on temperature, dimensions in mm (inch) Please note that guidance values may change due to local conditions. Please consider these potential changes particularly with respect to explosion protection. Also note that the accuracy of the transmitter also depends on the temperature in the connection head. SITRANS TS300 Clamp-on Design | | Measuring insert | - Special measuring insert made of stainless steel; hygienic design
- Measuring element made of silver, thermal decoupling through plastic insert
Measuring insert screwed into collar with spring tension. Use thermo-lubricant (see accessories) prior to mounting the device. | Tube collar | | Material | Temperature-resistant, high-performance plastic with integrated insulation system in hygienic design | Ambient temperature influence | Approx. 0.2%/10 K |
Process connection/protective tubeProcess parameters may only allow one specific technology for the selection of process connections. You also have to observe regional, standard-based and customer-specific requirements. The range of products therefore includes a broad selection of standard connections. In the case of redesigned or newly designed facilities, it is possible to achieve cost savings by implementing various measures: - Use of standard lengths through clever selection of screw-in, weld-in or flange sockets
- Moveable compression fittings
The temperature resistance of a material for process connections and protective tubes also limits the application area of the temperature sensor. The temperature range specified on the type plate always refers to the measuring insert, not the material which comes into contact with media. Two aspects must be considered when assessing temperature stability: - What maximum temperature may the material reach without a load?
- What is the behavior under load?
Process loadBecause of the large variety of possible applications and variables, it is not possible to make general binding statements regarding the resilience of components which comes into contact with media. The load diagrams below can be used for common applications. However, where operating conditions vary significantly, please contact our technical support team. Load on the protective tube and remedies: The process itself | Correction options |
---|
Temperature | Material selection | Pressure | Protective tube type | Flow velocity | Installation length, protective tube form | Viscosity | Installation length, protective tube form | Vibration | Support against vibration | Corrosiveness | Material selection, coating, covering | Abrasion (e.g. carbon dust) | Sensing rod, coating |
Load diagrams  Protective tubes with Ø9 x 1 mm (0.35 x 0.04), dimensions in mm (inch)  Protective tubes Ø12 x 2.5 mm (0.47 X 0.10 inch), dimensions in mm (inch)  Protective tubes Ø12 x 2.5 mm (0.47 X 0.10 inch), Ø14 x 2.5 mm (0.55 X 0.10 inch), dimensions in mm (inch)  Protective tubes Ø24 mm (0.95 inch), C= 65 mm (2.60 inch), dimensions in mm (inch)  Protective tubes Ø18 mm (0.71 inch), C= 65 mm (2.60 inch), dimensions in mm (inch)  Protective tubes Ø24 mm (0.95 inch), C= 125 mm (4.92 inch), dimensions in mm (inch) Protective tube calculation Properly applied load diagrams will provide a sufficient degree of safety for the protective tube dimensioning of most applications. However, there are cases in which operating conditions deviate too greatly from standard parameters. In this case a customized protective tube calculation may be required. Another reason for doing this calculation is the fact that flowing media can create turbulence at the tip of the protective tube under certain conditions. The protective tube will then vibrate and may even be destroyed if not configured correctly. This is the most frequent cause of protective tube failure. Siemens can offer protective tube calculations according to the two recognized procedures upon request. - Dittrich/Klotter method
- ASME PTC19.3-TW2016 method
This method also takes into account turbulence formation on a mathematical level.
Both methods provide a high degree of safety with regard to protective tube configuration, however, they do not provide a guarantee against breakdowns. A recalculation may be necessary in case of changes to the process parameters. Materials Material descriptions/Standards comparison | Max. temperature [°C (°F)] (unloaded) | Properties | Applications |
---|
Mat. No.: | AISI/Trade name: | EN 10028-2: | Description | | | | 1.4404 or 1.4435 | AISI 316 L | X2CrNiMo17-12-2 | Austenitic stainless steel | 600 (1112) | Good acid resistance, resistant against grain boundary corrosion | Chemical industry, waste treatment, paper and cellulose industry, food industry | 1.4571 | AISI 316 Ti | X6CrNiMoTi1712-2 | Austenitic stainless steel | 800 (1472) | Good acid resistance, resistant against grain boundary corrosion (supported by TI portion) | Chemical industry, textile industry, paper and cellulose industry, water supply, food and pharmaceuticals | 1.5415 | A 204 Gr.A | 16Mo3 | Carbon steel, high-alloy | 500 (932) | Resistant at higher temperatures, well suited for welding | Steam turbines, steam lines, water pipes | 1.7335 | A 182 F11 | 13CrMo4-5 | Carbon steel, high-alloy | 540 (1004) | Resistant at higher temperatures, well suited for welding | Steam turbines, steam lines, water pipes | 1.4841 | SS 314 | X15CrNiSi25-20 | Austenitic heat-resistant stainless steel | 1150 (2102) | Resistant at high temperatures, also resistant against low-O2 gases and gases containing nitrogen. | Flue gas, petrochemical industry, chemicals industry, power plants | 1.4762 | 446 | X10CrAl24 | Ferritic heat-resistant steel | 1150 (2102) | Resistant at high temperatures, in oxidizing and reducing sulfur-containing atmosphere | Chemical industry, power plants, steel industry, waste gas treatment | 2.4816 | Inconel 600 | NiCr15Fe | Nickel-chrome alloy | 1150 (2102) | Resistant at high temperatures, resistant against chlorine-induced cold crack corrosion | Chemical industry, petrochemical industry, food industry | 1.4876 | Incoloy 800 | X10NiCrAlTi32-21 | Austenitic heat-resistant stainless steel | 1100 (2012) | Excellent resistance against oxidation and carbonization at high temperatures, good corrosion resistance | O&G industry, waste gas treatment, power plants (steam boiler, heat exchanger), applications using aggressive fluids | 2.4819 | Hastelloy C 276 | NiMo16Cr15W | Nickel-Chrome-Molybdenum alloy | 1100 (2012) | Resistant at high temperatures, in oxidizing and reducing atmosphere, resistant against pitting and crevice corrosion, good corrosion resistance after welding | Chemicals industry, paper and cellulose industry, waste treatment, waste incinerators, emissions controls, shipbuilding and offshore industry | 2.4360 | Monel 400 | NiCu30Fe | Nickel-copper alloy | 500 (932) | Excellent corrosion resistance, particularly against chloride-induced cold crack corrosion | Chemical industry, offshore industry, nuclear technology, petrochemical industry |
Where cost-intensive materials are used with flange protective tubes, cost savings can be achieved by using a so-called flanged wheel. A thin disc of the material which comes into contact with media is applied prior to the flange (ordinary stainless steel). Materials of sensor tube/measuring insert: - SITRANS TSInsert, TS100, TS200
- Resistance thermometer Cr-Ni-Mo
- Thermocouple 2.4816/Inconel600
Vibration resistance of measuring insert, cable sensor Similar to the protective tube, the equipment also creates inner (Karman vortices) and outer vibration inducements which act on the measuring insert. For this reason, a special assembly of measurement elements is required. Other than a few exceptions for cable and compact thermometers, Siemens only produces sensors with a mineral-insulated plastic-sheathed cable. Together with precautions taken when installing the measuring element, the Siemens basic version already exceeds EN 60751 by more than a factor of 3. Pursuant to the measurement methods of this standard, the following values are obtained (tip-tip): - 10 g: Basic version and expanded measuring range
- 60 g: Increased vibration resistance and thermocouple
Bending ability of measuring insert / cable sensor All Siemens SITRANS TSinsert measuring inserts are made with a mineral-insulated plastic-sheathed cable (MIC). The same applies to a portion of the cable and compact thermometer. In addition to the already described properties, another advantage of the plastic-sheathed cable is its bending ability. This makes it possible to install these thermometers even in difficult to access areas. Ensure that the following minimum bending radius is observed: Ø MIC [mm] (inch) | Rmax = 4x Ø MIC [mm] (inch) |
---|
3 (0.12) | 12 (0.48) | 6 (0.24) | 24 (0.95) |
Where a smaller bending radius is required due to installation conditions, subsequent testing of the insulation resistance is recommended. Electrical stabilityInsulation resistance The insulation resistance between each measuring circuit and the fitting is tested at a voltage of 500 V DC at room temperature. Riso ≥ 100 MΩ Due to the property of the mineral-insulated cable, the insulation resistance decreases as temperature increases. Because of the special production method, it is however possible to achieve very good values even at high temperatures. Line resistance When connected to two-wire systems, the line resistance is included in the measurement result. The following rule of thumb can be used: - ∅ Measuring insert 3 mm (0.12 inch) 5 Ω/m or 12.8 °C (55.04 °F)
- ∅ Measuring insert 6 mm (0.24 in) 2.8 Ω/m or 7.1 °C (44.78 ℉)
For this reason a connection to three- or four-wire systems is highly recommended. ApprovalsExplosion protection Due to the variety of requirements, all flameproof versions, as well as those complying with CSA and FM are supplied without cable glands. Designator | Additional information | Region | Standard | Type of protection | For Zone | For Division |
---|
TSinsert TS100 TS200 | E00 | EU/AU/NZ | CE/RCM | Without Ex protection | | - | E17 | US/CA | cCSAus | - | E54 | CN | | - | E80 | EAC | TR | - | E01 | EU/AU/NZ | ATEX, IECEx | Intrinsic safety "i"/"IS" | 0…2/20…22 | - | E18 | US/CA | cCSAus | 0…2/20…22 | 1/2 | E55 | CN | NEPSI | 0…2/20…22 | - | E81 | EAC | EACEx | 0…2/20…22 | - | TS500 | E00 | EU/AU/NZ | CE/RCM | Without Ex protection | | - | E17 | US/CA | cCSAus | - | E54 | CN | | - | E80 | EAC | TR | - | E01 | EU/AU/NZ | ATEX, IECEx | Intrinsic safety "i"/"IS" | 0*…2/20*…22 | - | E18 | US/CA | cCSAus | 0*…2/20*…22 | 1/2 | E55 | CN | NEPSI | 0*…2/20*…22 | - | E81 | EAC | EACEx | 0*…2/20*…22 | - | E03 | EU/AU/NZ | ATEX, IECEx | Flameproof enclosure "d"/"XP" dust protection through housing "t"/"DIP" only with connection heads code AG0, AH0, AU0, AV0 | 0*…2/20*…22 | - | E20 (NPT) | US/CA | cCSAus | E21 (metric) | US | CSAus | 0*…2/20*…22 | 1/2 | E56 | CN | NEPSI | 0*…2/20*…22 | - | E82 | EAC | EACEx | 0*…2/20*…22 | - | E04 | EU/AU/NZ | ATEX, IECEx | Non-sparking "nA"/"NI" | 2 | - | E23 | US/CA | cCSAus | 2 | 2 | E57 | CN | NEPSI | 2 | - | E83 | EAC | EACEx | 2 | - | AU = Australia; CA = Canada; CN = China; EAC = Eurasian Customs Union; EU = Europe; US = USA |
* Zone 0 to process connection, outside Zone 1 Marine approvals Designator | Additional information | Approval |
---|
TSinsert TS100 TS200 TS500 | D01 | Det Norske Veritas Germanischer Lloyd (DNV GL) | D02 | Bureau Veritas (BV) | D04 | Lloyd’s Register of Shipping (LR) | D05 | American Bureau of Shipping (ABS) |
Pressure Equipment Directive: This device is not covered by the pressure equipment directive; classification as per the pressure equipment directive (DGRL 2014/68/EU), Directive 1/40; Section 1, Subsection 2.1.4. In addition, statutory, standards-based or operating specifications also require additional testing. The results are attested in certificates as per DIN EN 10204: - As per DIN EN 10204-2.1, order conformity (C35)
Certificate in which Siemens confirms that the delivered products correspond to the requirements of the order, without specification of test results. The testing does not have to be carried out on the delivered devices. - As per DIN EN 10204-3.1
Certificate in which Siemens confirms that the delivered products meet the requirements set out in the order, with indication of the specification of test results. Testing is carried out by an organization which is independent of production. The inspection certificate 3.1 replaces 3.1.B of the previous edition. - Material certificate for parts which come into contact with media (C12)
This certificate confirms the properties of the material and guarantees traceability up to the melting batch. - Pressure test (C31)
Hydrostatic pressure test on protective tube. Internal pressure for thread and weld-in, external pressure for flange forms. - Helium leak test (C32)
This test can be used to detect even the smallest leaks in protective tubes and welded seams. - Surface tear test (C33)
The color penetration method can detect tears and other surface defects. - Comparative test (calibration) (Y33)
The test object is measured in one temperature direction against a highly precise thermometer, and the measured values of test object and normal object are documented. However, calibration requires the measuring insert to be of a certain minimum length. Measuring inserts can be calibrated together with the associated transmitter. Calibration values can be stored in the transmitter in order to increase the accuracy of the system. - As per EN 10204-3.2
This type of acceptance certificate can be prepared on request, together with an acceptance representative of the ordering party or a representative indicated by official requirements (e.g. TÜV). It confirms that the delivered products meet the requirements set out in the order; it also contains the test results.
|
Deprecated: Function eregi() is deprecated in /home/h101150-2/siemens71.ru/docs/kip/kip.php on line 23
Deprecated: Function eregi() is deprecated in /home/h101150-2/siemens71.ru/docs/kip/kip.php on line 23
Deprecated: Function eregi() is deprecated in /home/h101150-2/siemens71.ru/docs/kip/kip.php on line 30
Deprecated: Function eregi() is deprecated in /home/h101150-2/siemens71.ru/docs/kip/kip.php on line 30
Deprecated: Function eregi() is deprecated in /home/h101150-2/siemens71.ru/docs/kip/kip.php on line 30
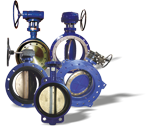
Deprecated: Function eregi() is deprecated in /home/h101150-2/siemens71.ru/docs/kip/kip.php on line 30
Deprecated: Function eregi() is deprecated in /home/h101150-2/siemens71.ru/docs/kip/kip.php on line 30
Àðìàòóðà DENDOR
Deprecated: Function eregi() is deprecated in /home/h101150-2/siemens71.ru/docs/kip/kip.php on line 23
Deprecated: Function eregi() is deprecated in /home/h101150-2/siemens71.ru/docs/kip/kip.php on line 30
Deprecated: Function eregi() is deprecated in /home/h101150-2/siemens71.ru/docs/kip/kip.php on line 30
Deprecated: Function eregi() is deprecated in /home/h101150-2/siemens71.ru/docs/kip/kip.php on line 30
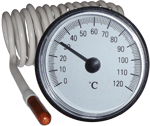
Deprecated: Function eregi() is deprecated in /home/h101150-2/siemens71.ru/docs/kip/kip.php on line 30
Deprecated: Function eregi() is deprecated in /home/h101150-2/siemens71.ru/docs/kip/kip.php on line 30
Äàò÷èêè è èçìåðèòåëè
Deprecated: Function eregi() is deprecated in /home/h101150-2/siemens71.ru/docs/kip/kip.php on line 23
Deprecated: Function eregi() is deprecated in /home/h101150-2/siemens71.ru/docs/kip/kip.php on line 30
Deprecated: Function eregi() is deprecated in /home/h101150-2/siemens71.ru/docs/kip/kip.php on line 30
Deprecated: Function eregi() is deprecated in /home/h101150-2/siemens71.ru/docs/kip/kip.php on line 30
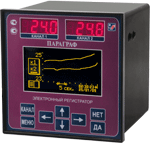
Deprecated: Function eregi() is deprecated in /home/h101150-2/siemens71.ru/docs/kip/kip.php on line 30
Deprecated: Function eregi() is deprecated in /home/h101150-2/siemens71.ru/docs/kip/kip.php on line 30
Ðåãóëÿòîðû è ðåãèñòðàòîðû
Deprecated: Function eregi() is deprecated in /home/h101150-2/siemens71.ru/docs/kip/kip.php on line 23
Deprecated: Function eregi() is deprecated in /home/h101150-2/siemens71.ru/docs/kip/kip.php on line 30
Deprecated: Function eregi() is deprecated in /home/h101150-2/siemens71.ru/docs/kip/kip.php on line 30
Deprecated: Function eregi() is deprecated in /home/h101150-2/siemens71.ru/docs/kip/kip.php on line 30
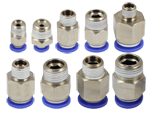
Deprecated: Function eregi() is deprecated in /home/h101150-2/siemens71.ru/docs/kip/kip.php on line 30
Deprecated: Function eregi() is deprecated in /home/h101150-2/siemens71.ru/docs/kip/kip.php on line 30
Ïíåâìàòè÷åñêîå îáîðóäîâàíèå
Deprecated: Function eregi() is deprecated in /home/h101150-2/siemens71.ru/docs/kip/kip.php on line 23
Deprecated: Function eregi() is deprecated in /home/h101150-2/siemens71.ru/docs/kip/kip.php on line 30
Deprecated: Function eregi() is deprecated in /home/h101150-2/siemens71.ru/docs/kip/kip.php on line 30
Deprecated: Function eregi() is deprecated in /home/h101150-2/siemens71.ru/docs/kip/kip.php on line 30
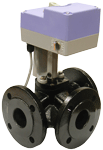
Deprecated: Function eregi() is deprecated in /home/h101150-2/siemens71.ru/docs/kip/kip.php on line 30
Deprecated: Function eregi() is deprecated in /home/h101150-2/siemens71.ru/docs/kip/kip.php on line 30
Êðàíû è Êëàïàíû
Deprecated: Function eregi() is deprecated in /home/h101150-2/siemens71.ru/docs/kip/kip.php on line 23
Deprecated: Function eregi() is deprecated in /home/h101150-2/siemens71.ru/docs/kip/kip.php on line 30
Deprecated: Function eregi() is deprecated in /home/h101150-2/siemens71.ru/docs/kip/kip.php on line 30
Deprecated: Function eregi() is deprecated in /home/h101150-2/siemens71.ru/docs/kip/kip.php on line 30
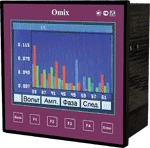
Deprecated: Function eregi() is deprecated in /home/h101150-2/siemens71.ru/docs/kip/kip.php on line 30
Deprecated: Function eregi() is deprecated in /home/h101150-2/siemens71.ru/docs/kip/kip.php on line 30
Èçìåðèòåëüíûå ïðèáîðû
Deprecated: Function eregi() is deprecated in /home/h101150-2/siemens71.ru/docs/kip/kip.php on line 23
Deprecated: Function eregi() is deprecated in /home/h101150-2/siemens71.ru/docs/kip/kip.php on line 30
Deprecated: Function eregi() is deprecated in /home/h101150-2/siemens71.ru/docs/kip/kip.php on line 30
Deprecated: Function eregi() is deprecated in /home/h101150-2/siemens71.ru/docs/kip/kip.php on line 30
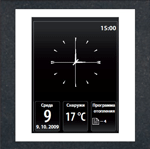
Deprecated: Function eregi() is deprecated in /home/h101150-2/siemens71.ru/docs/kip/kip.php on line 30
Deprecated: Function eregi() is deprecated in /home/h101150-2/siemens71.ru/docs/kip/kip.php on line 30
Ñèñòåìû áåñïðîâîäíîãî óïðàâëåíèÿ «óìíûé äîì»
Deprecated: Function eregi() is deprecated in /home/h101150-2/siemens71.ru/docs/kip/kip.php on line 23
Deprecated: Function eregi() is deprecated in /home/h101150-2/siemens71.ru/docs/kip/kip.php on line 30
Deprecated: Function eregi() is deprecated in /home/h101150-2/siemens71.ru/docs/kip/kip.php on line 30
Deprecated: Function eregi() is deprecated in /home/h101150-2/siemens71.ru/docs/kip/kip.php on line 30
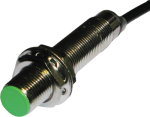
Deprecated: Function eregi() is deprecated in /home/h101150-2/siemens71.ru/docs/kip/kip.php on line 30
Deprecated: Function eregi() is deprecated in /home/h101150-2/siemens71.ru/docs/kip/kip.php on line 30
Áåñêîíòàêòíûå âûêëþ÷àòåëè Êîíå÷íûå âûêëþ÷àòåëè Îïòè÷åñêèå äàò÷èêè Ýíêîäåðû
Deprecated: Function eregi() is deprecated in /home/h101150-2/siemens71.ru/docs/kip/kip.php on line 23
Deprecated: Function eregi() is deprecated in /home/h101150-2/siemens71.ru/docs/kip/kip.php on line 30
Deprecated: Function eregi() is deprecated in /home/h101150-2/siemens71.ru/docs/kip/kip.php on line 30
Deprecated: Function eregi() is deprecated in /home/h101150-2/siemens71.ru/docs/kip/kip.php on line 30
Deprecated: Function eregi() is deprecated in /home/h101150-2/siemens71.ru/docs/kip/kip.php on line 30

Deprecated: Function eregi() is deprecated in /home/h101150-2/siemens71.ru/docs/kip/kip.php on line 30
SKW-FS - Óñòàíîâêà óìÿã÷åíèÿ
Deprecated: Function eregi() is deprecated in /home/h101150-2/siemens71.ru/docs/kip/kip.php on line 23
Deprecated: Function eregi() is deprecated in /home/h101150-2/siemens71.ru/docs/kip/kip.php on line 30
Deprecated: Function eregi() is deprecated in /home/h101150-2/siemens71.ru/docs/kip/kip.php on line 30
Deprecated: Function eregi() is deprecated in /home/h101150-2/siemens71.ru/docs/kip/kip.php on line 30
Deprecated: Function eregi() is deprecated in /home/h101150-2/siemens71.ru/docs/kip/kip.php on line 30
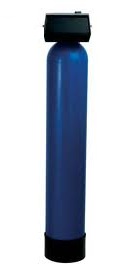
Deprecated: Function eregi() is deprecated in /home/h101150-2/siemens71.ru/docs/kip/kip.php on line 30
SKW-FK - Óñòàíîâêà îáåçæåëåçèâàíèÿ
|