![]() B48 |
Documentation, production flowcharts | B43 | B45 | |
---|---|---|---|
Generated once | B43 | – | |
Updated every month | B45 | – |
– | Options mutually exclude each other. |
Options B43 and B45 provide production flowcharts. These will be sent by e-mail following receipt of order either in MPP format (Microsoft Project) or in PDF format (English/German) as required. Please select format.
Option | Description |
---|---|
B43 | Production flowchart: Generated once |
B45 | Production flowchart: Updated every month |
C36, C38, C43, C48 and Y36
External auxiliary power supply
With options C36, C38, C43, C48 and Y36, a connection terminal is available to the customer that can be used to supply loads (cabinet fan, cabinet heater, cabinet lighting, PLC, etc.) from an external power source. The supply system type for options C36, C38, C43, and C48 is grounded (TN/TT system). Only one phase is protected using a suitable miniature circuit breaker. Different voltages and supply system types are defined using option Y36. Please specify additional protection or connection of the N conductor (prescribed in certain countries).
Auxiliary DC voltage on request.
Option | Description |
---|---|
C36 | Connection of 230 V 1 AC 50 Hz auxiliary voltage provided by the customer |
C38 | Connection of 400 V 3 AC 50 Hz auxiliary voltage provided by the customer |
C43 | Connection of 500 V 3 AC 50 Hz auxiliary voltage provided by the customer |
C48 | Connection of 690 V 3 AC 50 Hz auxiliary voltage provided by the customer |
Y36 | Connection of different level of 3-phase AC voltage provided by the customer; please specify voltage |
C56, C57 and Y55
External control voltage supply
Inadmissible option combinations C56, C57 and Y55
External control voltage supply | C56 | C57 | Y55 | |
---|---|---|---|---|
Connection of 230 V 1 AC 50 Hz control voltage provided by the customer, no UPS backup | C56 | – | – | |
Connection of 230 V 1 AC 50 Hz control voltage provided by the customer; UPS backup | C57 | – | – | |
Connection of different level of single-phase AC voltage provided by the customer; please specify voltage | Y55 | – | – |
– | Options mutually exclude each other. |
With options C56, C57 and Y55, an external current source is defined for the converter. This is necessary in the following situations:
- If the display should indicate correctly even though no line voltage is present and the converter should not indicate a fault.
- The initialization time for the converter of approximately 3 s for temporary power failures does not apply in the case of an external, backed-up control voltage (precharging and synchronization time, however, remain unaffected).
If no external control voltage supply is selected, the converter will be supplied from the DC link in the case of compact units without a main contactor. For the following compact units, an additional board is required for mains supply backup (option E85):
Type | Converter type |
6SE0100?1A?23?4?A7 | 2T2A?07600?030 |
6SE0100?1A?24?2?A7 | 2T2A?07600-037 |
6SE0100?1A?25?0?A7 | 2T2A?07600-045 |
6SE0100?1A?25?8?A7 | 2T2A?07600-055 |
6SE0100?1A?28?0?A7 | 2T2A?07600?075 |
6SE0100?1A?31?0?A7 | 2T2A?07600?090 |
6SE0100?1A?31?2?A7 | 2T2A?07600?110 |
6SE0100?1A?31?4?A7 | 2T2A?07600?132 |
6SE0100?1A?31?7?A7 | 2T2A?07600?160 |
6SE0100?1A?32?1?A7 | 2T2A?07600?200 |
For cabinet units with and without input contactors and for cabinet systems with input contactors, the control voltage is generated from the converter line voltage by a control transformer.
Advantage:
When the converter control voltage is supplied from the DC link, this provides a backup function for drives with a coupled rotating mass (e.g. fan drive). This means that the DC link of the converter is maintained for a short time in the case of a temporary voltage drop or power failure due to continued rotation of the rotating mass on the motor. The control voltage for the converter is backed-up until the DC link voltage fails due to standstill of the rotating mass, or until the parameter "t-restart" causes switch-off.
Option | Description |
---|---|
C56 | Connection for 230 V 1 AC 50 Hz external control voltage provided by the customer, no UPS backup |
C57 | Connection for 230 V 1 AC 50 Hz external control voltage provided by the customer, with UPS backup |
Y55 | Connection for different level of single-phase AC control voltage with 47 to 63 Hz provided by the customer, please specify voltage |
D01, D02, D04, D05 and D06
Converter documentation
For the scope of the converter documentation, see the "Documentation" section under "Services and documentation". A CD comprising a manual and IMS is supplied with every converter.
Option | Description |
---|---|
D01 | Manual and set of diagrams in PDF format per e-mail, German/English |
D02 | Manual in PDF format, set of diagrams in DXF format per e-mail, German/English |
D04 | Manual and set of diagrams, single hardcopy, German/English |
D05 | Manual and set of diagrams in PDF format on CD, German/English |
D06 | Manual in PDF format, set of diagrams in DWG format on CD, German/English |
Note:
Please ask your Siemens sales partner if the documentation or set of diagrams are required in a different language.
G13, G14, G15, G16 and G18
Accessories for IMS (Inverter Management Software)
G13 USB PROFIBUS interface (supplied separately packed)
G13 Softing PROFIBUS (PROFIBUS interface)
Active single-channel USB high-speed interface for connecting a PC with IMS to a PROFIBUS network. The interface is suitable for control and visualization tasks as well as for parameterization and analysis applications via the IMS. All SINAMICS G180 converters in the PROFIBUS network can be addressed.
No additional power connection is required for this converter. The cable on the converter has a double PROFIBUS SUB-D 9-pin connection (socket/plug with end wiring) for connecting to PROFIBUS. As a result, a simple connection is possible directly on the SINAMICS G180 with PROFIBUS board (G01).
Note:
The installation notes in the help function of IMS must be observed.
G14 Ethernet-PROFIBUS gateway
G14 Softing FG-100PB
Gateway between host systems on Ethernet and the PROFIBUS bus system. Suitable for network configuration, device parameterization or acquisition of operating data. All SINAMICS G180 converters in the PROFIBUS system can be monitored and parameterized.
The Ethernet-PROFIBUS gateway can be installed in the converter cabinet or supplied separately packed. Please specify your requirements in the order. The gateway is normally installed at the most favorable transition point between Ethernet and PROFIBUS.
Technical data:
- Dimensions (W ? H ? D) 47 ? 131 ? 11 mm
- Mounting on 35 mm DIN rail
- Power supply 24 V DC (±20 %); 0.3 A
- Operating temperature 0 °C to 55 °C
Scope of supply:
- Ethernet interface on PROFIBUS
- Installation manual
- CD with Windows drivers
Note:
The installation notes in the help function of IMS must be observed.
If the Ethernet-PROFIBUS gateway is supplied separately with the converter, a separately power supply unit is required. This is not part of the scope of supply.
G15 Ethernet to RS232/485/422 converter (supplied separately packed)
With option G15 a serial/Ethernet converter is supplied separately packed. If several converters are interconnected over an RS485 network, up to 128 converters can be connected to Ethernet using one converter.
Technical data:
- Dimensions (W ? H ? D) 151 ? 75 ? 26 mm
- Power supply 10 to 30 V DC; 1.6 W
Note:
The installation notes in the help function of IMS must be observed.
An external power supply unit is required for the Ethernet to RS232/485/422 converter which is not part of the scope of supply.
G16 USB cable A/B, 2 m (supplied separately packed)
G16 USB cable A/B (example shown)
Option G16 comprises a 2 m long USB cable for parameterizing the SINAMICS G180 from the IMS.
G18 USB connector on front of control cabinet door
G18 USB connector on front of control cabinet door (example shown)
With option G18 a USB connector is installed in the control cabinet door that allows the converter to be parameterized from the IMS without having to open the cabinet door. IP65 degree of protection.
M96, M93 and M94
Marking of cable cores and items of equipment
Inadmissible option combinations M93 and M94
Marking of cable cores and | M96 | M93 | M94 | |
---|---|---|---|---|
Dual marking of items of equipment | M96 | ? | ? | |
Cable marking, C-type | M93 | ? | – | |
Cable marking (shrink-on sleeve) | M94 | ? | – |
? | Options are combinable. |
– | Options mutually exclude each other. |
M96 Dual marking of items of equipment
M96 Example of dual marking of items of equipment
With option M96 the items of equipment are marked twice, once on the equipment and once directly adjacent to the mounting location of the equipment.
M93 Cable marking, C-type
M93 Example of cable marking, C-type
- Cable markings in the shape of the letter C are clipped onto the control cables.
- Larger power cables are labeled using shrink-on sleeves.
- The terminal designation only is numbered on the cable and not the item designation.
Example:
Terminal –X2:41 > Cable is marked with 41.
M94 Cable marking (shrink-on sleeve)
M94 Example of cable marking
- Cable markings using shrink-on sleeves are attached to the cables.
- The terminal designation and the item designation are labeled on the cable.
Example:
Terminal –X2:41 > Cable is marked with –X2:41.
E85
Board for mains supply backup
To enable the control voltage to be generated from the DC link for the following converter types, option E85 (series-connected power supply unit for mains supply backup) is required.
This option must be ordered separately for all cabinet units and for the following compact units:
Type | Converter type |
---|---|
6SE0100?1A?23?4?A7 | 2T2A?07600?030 |
6SE0100?1A?24?2?A7 | 2T2A?07600?037 |
6SE0100?1A?25?0?A7 | 2T2A?07600?045 |
6SE0100?1A?25?8?A7 | 2T2A?07600?055 |
6SE0100?1A?28?0?A7 | 2T2A?07600?075 |
6SE0100?1A?31?0?A7 | 2T2A?07600?090 |
6SE0100?1A?31?2?A7 | 2T2A?07600?110 |
6SE0100?1A?31?4?A7 | 2T2A?07600?132 |
6SE0100?1A?31?7?A7 | 2T2A?07600?160 |
6SE0100?1A?32?1?A7 | 2T2A?07600?200 |
Advantage:
When the converter control voltage is supplied from the DC link, this provides a backup function for drives with a coupled rotating mass (e.g. fan drive). This means that the DC link of the converter is maintained for a short time in the case of a temporary voltage drop or power failure due to continued rotation of the rotating mass on the motor. The control voltage for the converter is therefore backed up for a short time.
G01, G12, G20, G22 and G27
Additional boards for bus connection
Inadmissible option combinations G01, G20, G22, G27
Additional boards for bus connection | G01 | G12 | G20 | G22 | G27 | |
---|---|---|---|---|---|---|
Board for PROFIBUS DPV1 | G01 | ? | – | – | – | |
PROFIBUS expansion module for option G10 or G11 | G12 | ? | ? | ? | ? | |
Board for CANopen | G20 | – | ? | – | – | |
Board for Modbus RTU | G22 | – | ? | – | – | |
Board for Modbus TCP | G27 | – | ? | – | – |
? | Options are combinable. |
– | Options mutually exclude each other. |
G01 Board for PROFIBUS DPV1
G01 PROFIBUS board for SINAMICS G180 in compact unit
G01 PROFIBUS board for SINAMICS G180 in cabinet unit
Option G01 for the PROFIBUS DPV1 board is suitable for cyclic and non-cyclic data transfer and can be retrofitted in compact units and cabinet units at any time.
G12 PROFIBUS expansion module for option G10 or G11 (SENTRON PAC3200 power monitoring device)
G12 PROFIBUS expansion module
Option G12 allows the SENTRON PAC3200 power monitoring device to be connected to PROFIBUS. This expansion module can only be ordered in conjunction with option G10 or G11.
G20 Board for CANopen
G20 CANopen
Option G20 (board for CANopen) transfers data in binary form. Fieldbus connection is implemented in accordance with the CANopen standard. This board can be retrofitted in compact units and cabinet units at any time, provided that no other bus system has been installed beforehand.
G22 Board for Modbus RTU
G22 Modbus RTU
Option G22 (board for Modbus RTU) transfers data in binary form. This board can be retrofitted in compact units and cabinet units at any time, provided that no other bus system has been installed beforehand.
G27 Board for Modbus TCP
G27 Modbus TCP
Option G27 (board for Modbus TCP) is very similar to Option G22 (board for Modbus RTU), except that TCP packages are used to send the data. This board can be retrofitted in compact units and cabinet units at any time, provided that no other bus system has been installed beforehand.
G02, G03, G04 and G05
Peripheral boards 1 to 4
Inadmissible option combinations G02, G03, G04 and G05
Peripheral board 1 … 4 | G02 | G03 | G04 | G05 | |
---|---|---|---|---|---|
Peripheral board 1 | G02 | – | – | – | |
Peripheral board 2 | G03 | – | – | – | |
Peripheral board 3 | G04 | – | – | – | |
Peripheral board 4 | G05 | – | – | – |
– | Options mutually exclude each other. |
The functionality of the converter is expanded with the peripheral board. Every converter can be fitted or even retrofitted with one of these peripheral boards.
Boards with safety-related inputs (PTC thermistor or the function "Safe Torque Off") are only permitted to be retrofitted by our authorized qualified personnel.
In addition to the main board, peripheral boards 2 and 4 are also expanded by a daughterboard which contains the circuitry for the PTC thermistor inputs.
Peripheral board | ||||
---|---|---|---|---|
1 | 2 | 3 | 4 | |
2 PTC thermistor inputs for ATEX-certified motor temperature monitoring for motors in hazardous zones (prewarning/trip) | ? | ? | ||
One input "Safe Torque Off" acc. to EN ISO 13849?1, Cat. 3. PL d or SIL 2 acc. to EN 61508 | ? | ? | ||
9 digital inputs (DI) | ? | ? | ||
3 relay outputs (DO) | ? | ? | ||
2 analog outputs (AO) | ? | ? | ? | ? |
24 V / 300 mA power supply unit | ? | ? |
G02 Peripheral board 1
G02 Peripheral board 1
Option G02 (peripheral board 1) provides in addition to standard converter terminals:
- 2 analog outputs (AO) 4 to 20 mA/0 to 10 V
Standard assignment of inputs/outputs
The table below provides an overview of the pre-assignment function of interfaces in the pin assignments for the "Standard" application.
Signal designation | Function |
---|---|
Internal PTC thermistor input 90, 91, 92, 93 | Not assigned |
Internal analog output 64, 65 | Torque |
Internal analog output 66, 67 | Power |
G02 Circuit diagram for peripheral board 1
G03 Peripheral board 2
G03 Peripheral board 2 in the compact unit
Option G03 (peripheral board 2) provides in addition to standard converter terminals:
- 2 analog outputs (AO) 4 to 20 mA/0 to 10 V
- 2 PTC thermistor inputs for ATEX-certified motor temperature monitoring for motors in hazardous zones (prewarning/trip)
- PTC thermistor monitoring without contactor through monitoring unit integrated in converter, certified to SIL 1 in accordance with EN 61508
The converter controller processes the signal of the peripheral board. In the event of excessive motor temperature, or the function "Safe Torque Off", the converter inhibits the firing signals of the IGBTs. The voltage supply of the driver stages is also switched off. These two redundant, diverse and self-monitored switch-off paths ensure that the power infeed to the motor is safely interrupted. Further heating or rotation of the motor is excluded. The converter can only be reset or switched on when the motor has cooled down sufficiently and the fault has been acknowledged. When the voltage fails, the converter safely interrupts the power infeed to the motor, because firing signals are no longer transferred. If a fault was active at the moment of power failure, the converter will also be in fault status when power is restored.
Standard assignment of inputs/outputs
The table below provides an overview of the pre-assignment function of interfaces in the pin assignments for the "Standard" application.
Signal designation | Function |
---|---|
Internal PTC thermistor input 90, 91 | PTC thermistor for disconnection (ATEX-certified) |
Internal PTC thermistor input 92, 93 | PTC thermistor for warning |
Internal analog output 64, 65 | Torque |
Internal analog output 66, 67 | Power |
G03 Circuit diagram for peripheral board 2
G04 Peripheral board 3
G04 Peripheral board 3 in the compact unit
Option G04 (peripheral board 3) provides in addition to standard converter terminals:
- 2 analog outputs (AO) 4 to 20 mA/0 to 10 V
- One digital input "Safe Torque Off" (STO, single-channel or two-channel) acc. to EN ISO 13849?1, Cat. 3 or SIL 2 acc. to EN 61508
9 digital inputs (DI) - 3 relay outputs (DO)
In addition, the relay outputs here are not only isolated from the converter electronics but also from each other. - 24 V / 300 mA power supply unit
SIL 2 (acc. to EN 61508) – STO (Safe Torque Off).
Safe Torque Off (STO) function implemented according to SIL 2 to EN 61508.
The "Safe Torque Off" (STO) function has a redundant switch-off path in the converter. The implementation is performed using hardware. A relay in the power unit of the converter disconnects the power supply of the IGBT driver. A second circuit, also via hardware, produces a controller disable.
The "Safe Torque Off" input can be implemented with either one or two channels. The board is coded for single-channel activation at the factory. If two-channel activation is required, please specify this in the order. Digital input X2:24 is reserved for the two-channel version.
Standard assignment of inputs/outputs
The table below provides an overview of the pre-assignment function of interfaces in the pin assignments for the "Standard" application.
Signal designation | Function |
---|---|
Internal digital input 19, 20 | 24 V DC; "Safe Torque Off" acc. to EN ISO 13849?1, Cat. 3; or SIL 2 acc. to EN 61508 |
Internal digital input 6, 7, 21, 22, 23, 24, 25, 26 | Freely parameterizable |
Internal PTC thermistor input 90, 91, 92, 93 | Not assigned |
Internal digital output 43, 44, 45 | Relay 5: "Motor temperature trip" |
Internal digital output 46, 47 | Relay 6: "Automatic mode (normal)" |
Internal digital output 48, 49 | Relay 7: "Speed 0" |
Internal analog output 64, 65 | Torque |
Internal analog output 66, 67 | Power |
NAMUR-compliant assignment of inputs/outputs
The table below provides an overview of the pre-assignment function of interfaces in the pin assignments for the "NAMUR" application.
Signal designation | Function |
---|---|
Internal digital input 17, 18 | Forced power supply disconnection |
Internal digital input 19, 20 | +24 V DC; forced inverter inhibit |
Internal digital input 6 | Rapid stop global 1 |
Internal digital input 7 | Separately driven fan of motor activated |
Internal digital input 21 | External fault |
Internal digital input 22 | External warning |
Internal digital input 23 | Operation, bus |
Internal digital input 24 | Controller ON |
Internal digital input 25 | Fixed setpoint 1 |
Internal digital input 26 | Fixed setpoint 2 |
Internal PTC thermistor input 90, 91, 92, 93 | Not assigned |
Internal digital output 43, 44, 45 | Relay 5: "Motor temperature trip" |
Internal digital output 46, 47 | Relay 6: "Automatic mode (normal)" |
Internal digital output 48, 49 | Relay 7: "Speed 0" |
Internal analog output 64, 65 | Torque |
Internal analog output 66, 67 | Power |
G04 Circuit diagram for peripheral board 3
G05 Peripheral board 4
G05 Peripheral board 4 in the compact unit
G05 Peripheral board 4 in the cabinet unit
Option G05 (peripheral board 4) provides in addition to the standard terminals:
- 2 analog outputs (AO) 4 to 20 mA/0 to 10 V
- 2 PTC thermistor inputs, one certified for ATEX (disconnection), one warning for motor temperature monitoring of motors in a hazardous area
- One digital input "Safe Torque Off" acc. to EN ISO 13849?1, Cat. 3/(STO) implemented according to SIL 2 acc. to EN 61508
9 digital inputs (DI) - 3 relay outputs (DO)
In addition, the relay outputs here are not only isolated from the converter electronics but also from each other. - 24 V / 300 mA power supply unit
- ATEX-certified PTC thermistor monitoring without contactor through monitoring unit integrated in converter, certified to SIL 1 in accordance with EN 61508
PTC thermistor monitoring without contactor through monitoring unit integrated in converter, certified to SIL 1 in accordance with EN 61508 or Category 2, PL c in accordance with EN ISO 13849?1
The converter controller processes the signal of the peripheral board. In the event of excessive motor temperature, or the function "Safe Torque Off", the converter inhibits the firing signals of the IGBTs. The voltage supply of the driver stages is also switched off. These two switch-off paths ensure that the power infeed to the motor is immediately interrupted. Further heating or rotation of the motor is excluded. The converter can only be reset or switched on when the motor has cooled down sufficiently. When the voltage fails, the converter safely interrupts the power infeed to the motor, because firing signals are no longer transferred. If a fault was active at the moment of power failure, the converter will also be in fault status when power is restored.
SIL 2 (acc. to EN 61508) – STO (Safe Torque Off).
Safe Torque Off (STO) function implemented according to SIL 2 to EN 61508.
The "Safe Torque Off" (STO) function has a redundant switch-off path in the converter. The implementation is performed using hardware. A relay in the power unit of the converter disconnects the power supply of the IGBT driver. A second circuit, also via hardware, produces a controller disable. Both switch-off paths are based on the closed-circuit principle, i.e. a failure of the control voltage results in shutdown of the converter.
The "Safe Torque Off" input can be implemented with either one or two channels. The board is coded for single-channel activation at the factory. If two-channel activation is required, please specify this in the order. Digital input X2:24 is reserved for the two-channel version.
Subsequent changeover from single-channel to two-channel is only permitted to be implemented by our authorized qualified personnel.
Standard assignment of inputs/outputs
The table below provides an overview of the pre-assignment function of interfaces in the pin assignments for the "Standard" application.
Signal designation | Function |
---|---|
Internal digital input 19, 20 | 24 V DC; "Safe Torque Off" acc. to EN ISO 13849?1, Cat. 3; or SIL 2 acc. to EN 61508 |
Internal digital input 6, 7, 21, 22, 23, 24, 25, 26 | Freely parameterizable |
Internal PTC thermistor input 90, 91 | PTC thermistor for disconnection (ATEX-certified) |
Internal PTC thermistor input 92, 93 | PTC thermistor for warning |
Internal digital output 43, 44, 45 | Relay 5: "Motor temperature trip" |
Internal digital output 46, 47 | Relay 6: "Automatic mode (normal)" |
Internal digital output 48, 49 | Relay 7: "Speed 0" |
Internal analog output 64, 65 | Torque |
Internal analog output 66, 67 | Power |
NAMUR-compliant assignment of inputs/outputs
The table below provides an overview of the pre-assignment function of interfaces in the pin assignments for the "NAMUR" application.
Signal designation | Function |
---|---|
Internal digital input 17, 18 | Forced power supply disconnection |
Internal digital input 19, 20 | +24 V DC; forced inverter inhibit |
Internal digital input 6 | Rapid stop global 1 |
Internal digital input 7 | Separately driven fan of motor activated |
Internal digital input 21 | External fault |
Internal digital input 22 | External warning |
Internal digital input 23 | Operation, bus |
Internal digital input 24 | Controller ON |
Internal digital input 25 | Fixed setpoint 1 |
Internal digital input 26 | Fixed setpoint 2 |
Internal PTC thermistor input 90, 91 | PTC thermistor for disconnection (ATEX-certified) |
Internal PTC thermistor input 92, 93 | PTC thermistor for warning |
Internal digital output 43, 44, 45 | Relay 5: "Motor temperature trip" |
Internal digital output 46, 47 | Relay 6: "Automatic mode (normal)" |
Internal digital output 48, 49 | Relay 7: "Speed 0" |
Internal analog output 64, 65 | Torque |
Internal analog output 66, 67 | Power |
G05 Circuit diagram for peripheral board 4
G10, G11, K14, K15 and K37
Control elements and display instruments in control cabinet door
Inadmissible option combinations G10 and G11
Control elements and display instruments in cabinet door | G10 | G11 | K14 | K15 | K37 | |
---|---|---|---|---|---|---|
SENTRON PAC3200 power monitoring device (without current transformer) | G10 | – | ? | ? | ? | |
SENTRON PAC3200 power monitoring device (with current transformer) | G11 | – | ? | ? | ? | |
External 4-line operator panel, supplied separately packed | K14 | ? | ? | ? | ? | |
External 4-line operator panel integrated in control cabinet door | K15 | ? | ? | ? | ? | |
Selector switch in form of key-operated switch | K37 | ? | ? | ? | ? |
? | Options are combinable. |
– | Options mutually exclude each other. |
G10 SENTRON PAC3200 power monitoring device (without current transformer)
G10 and G11 Line voltage display, Siemens SENTRON PAC3200
Option G10 comprises the Siemens SENTRON PAC3200 power monitoring device without current transformer. This device is built into the cabinet door and fully wired up.
Display of:
- Line voltage
- Line frequency
Degree of protection: IP65
Dimensions (H ? W ? D): 96 ? 96 ? 51 mm
With option G12 (PROFIBUS expansion module) the SENTRON PAC3200 can be connected to PROFIBUS.
G11 SENTRON PAC3200 power monitoring device (with current transformer)
For picture, see option G10 "SENTRON PAC3200 power monitoring device (without current transformer)".
Option G11 comprises the Siemens SENTRON PAC3200 power monitoring device with current transformer. This device is built into the cabinet door and fully wired up.
Display of:
- Line current
- Line voltage
- Line frequency
- Power factor
- Line harmonic THD for U and I
- Apparent power
- Reactive power
- Active power
- Apparent/reactive/active energy
Degree of protection: IP65
Dimensions (H ? W ? D): 96 ? 96 ? 51 mm
With option G12 (PROFIBUS expansion module) the SENTRON PAC3200 can be connected to PROFIBUS.
Note:
A larger cabinet or additional cabinet may have to be planned for the current transformer.
K14 External 4-line operator panel, supplied separately packed
K14 and K15 external operator panel
Compact units have an internal display. Using option K14 an external display can be ordered that can be built into a door or operator panel by the customer (max. distance with external 24 V DC power supply: 1000 m).
Degree of protection: IP54
Dimensions (H ? W ? D): 96 ? 144 ? 61 mm
K14 Dimension drawing of external operator panel
Note:
Without an external 24 V DC supply, the permitted length of the cable is max. 5 m (a shielded twisted-pair cable must be used as the connecting cable, e.g. LiYCY 2?2?0.25).
With option K14 a 5 m long connecting cable is supplied.
If the cable between the converter and the operator panel is longer than 5 m, an external 24 V DC power supply unit will be required.
K15 External 4-line operator panel integrated in control cabinet door
For picture, see option K14 "External 4-line operator panel, supplied separately packed".
Compact units have an internal display. Using option K15 an external display can be ordered that is built into the cabinet door in the case of cabinet systems. Cabinet units generally have a display in the door.
Note:
An "internal operator panel" can be requested in place of the external operator panel (in the cabinet door of air-cooled cabinet units), see "Engineer To Order – ETO" under "Option descriptions".
Option M55 is used for this in the case of liquid-cooled cabinet units.
K37 Selector switch in form of key-operated switch
K37 Key-operated switch (example shown)
With option K37 the selector switches that are built into the cabinet door are implemented as key-operated switches (e.g. local/remote switches). The switches must be explicitly specified in the order.
L00 and L02
RFI suppression filter
Inadmissible option combinations L00 and L02
RFI suppression filter | L00 | L02 | |
---|---|---|---|
RFI suppression filter EN 55011 Class A | L00 | – | |
RFI suppression filter EN 55011 Class B | L02 | – |
– | Options mutually exclude each other. |
L00 RFI suppression filter Category C2 or C3 (Class A)
Option L00 comprises an RFI suppression filter of Class A. This fulfills the following requirements:
- For compact units in a TN/TT system:
RFI suppression filter acc. to EN 55011 Class A and EMC product standard EN 61800?3 Category C2 (environment 1, public network) - For cabinet units in a TN/TT system:
RFI suppression filter acc. to EN 55011 Class A and EMC product standard EN 61800?3 Category C3 (environment 2, industrial area)
Note:
Option L00 is only permitted to be installed for devices that are intended for use in grounded networks, i.e. for 400 V devices (only permitted to be used in grounded systems) and for 500 V or 690 V devices that operate on a grounded line voltage.
For units in category C2 the following applies:
If not correctly installed and commissioned, this product can cause radio frequency interference in residential areas. In this case, it may be necessary for the operator of the unit to take further interference suppression measures.
L02 RFI suppression filter EN 55011 Class B
Option L02 comprises an RFI suppression filter of Class B. This fulfills the following requirements for compact units:
RFI suppression filter acc. to EN 55011 Class B and EMC product standard EN 61800?3 Category C1 (environment 1, residential area).
Note:
Option L02 is only permitted to be installed for devices that are intended for use in grounded networks, i.e. for 400 V devices (only permitted to be used in grounded systems) and for those that operate on a grounded line voltage.
L03 and L04
Line Harmonics Filter
L03/L04 Example of a Line Harmonics Filter in the cabinet unit
L03/L04 Example of a Line Harmonics Filter in the converter cabinet with compact unit
Inadmissible option combinations L03 and L04
Line Harmonics Filter | L03 | L04 | |
---|---|---|---|
Line Harmonics Filter for 50 Hz line frequency | L03 | – | |
Line Harmonics Filter for 60 Hz line frequency | L04 | – |
– | Options mutually exclude each other. |
L03 Line Harmonics Filter for 50 Hz line frequency
With option L03 a Line Harmonics Filter for 50 Hz line frequency will be installed in the control cabinet for reducing the line-side harmonics or for compliance with IEEE 519. See the general technical data.
Note:
Please ask your Siemens contact person for the exact cabinet dimensions.
L04 Line Harmonics Filter for 60 Hz line frequency
With option L04 a Line Harmonics Filter for 60 Hz line frequency will be installed in the control cabinet for reducing the line-side harmonics or for compliance with IEEE 519. See the general technical data.
Note:
Please ask your Siemens contact person for the exact cabinet dimensions.
L10, L14, L15, L16 and L17
Output filter
Inadmissible option combinations L14, L15, L16, L17
Output filter | L10 | L14 | L15 | L16 | L17 | |
---|---|---|---|---|---|---|
Strengthened dv/dt output filter | L10 | ? | ? | ? | ? | |
Sine-wave filter in control cabinet, 75 Hz; 10 % voltage drop | L14 | ? | – | – | – | |
Sine-wave filter in control cabinet, 60 Hz; 10 % voltage drop | L15 | ? | – | – | – | |
Sine-wave filter IP00 supplied separately, 75 Hz; 10 % voltage drop | L16 | ? | – | – | – | |
Sine-wave filter in control cabinet, 75 Hz; 5 % voltage drop | L17 | ? | – | – | – |
? | Options are combinable. |
– | Options mutually exclude each other. |
L10 Strengthened dv/dt output filter for max. 250/300 m (type-dependent) – design for longer motor cables available on request
L10 Output filter (example of filter reactor)
All SINAMICS G180 converters are fitted with a dv/dt filter as standard that are suitable for motor cable lengths (depending on the power rating, see technical data) from 100 to 200 m typically. Standard motors with standard insulation can be used.
With option L10 a strengthened dv/dt output filter is selected. The strengthened dv/dt output filter typically extends the possible motor cable length (depending on the power rating, see technical data) as follows:
- Shielded cables: 250 to 300 m (e.g. NYCWY)
- Unshielded cables: 300 to 450 m (e.g. NYY)
These cable lengths are based on worst-case conditions. If the motor cable lengths are longer in a special case, the feasibility can be checked in the factory. The cable types, their number and length must be known for this purpose.
Method of operation:
The dv/dt filter in SINAMICS G180 limits the voltage gradient (dv/dt) and the peak voltage ULL for the motor winding to the following values:
- Voltage gradient dv/dt < 1500 V/µs
- Peak voltages ULL (typically) < 1560 V
Various explosion protection regulations (ATEX) specify a maximum permissible average peak voltage at the motor (IEC 60034?25?A) of 1560 V (LHX2 motor winding) and a permissible maximum terminal voltage at the motor (explosion-proof motors only) of 1866 V.
Design:
SINAMICS G180 dv/dt filters mainly comprise a dv/dt reactor and a voltage limiting network that limits the voltage peaks.
Reduction of voltage peaks using dv/dt filters normally obviates the need for special insulation of the motors. The filter also has a positive effect on the bearing currents (reduction of bearing currents).
Voltage drop:
The voltage drop in the converter is compensated using the "Overmodulation" software function in which case the output voltage of the converter is almost equal to the input voltage.
L14 Sine-wave filter integrated in control cabinet or additional cabinet, suitable for motor frequencies of ? 75 Hz, voltage drop approx. 10 % of the line voltage
L14 Sine-wave filter (example shown)
With option L14 a sine-wave filter for motor frequencies of ? 75 Hz is integrated in the control cabinet.
Sine-wave filters should largely suppress the clock-frequency harmonics at the motor terminals to the extent that the voltage approximates a sinusoidal wave. They are implemented as LC networks.
Due to the large voltage drop of a sine-wave filter, it should normally be checked before it is used whether a dv/dt filter would suffice for the application case. To check this, please send the necessary data (cable length, cable type, cable cross-section, number of parallel cables) to your Siemens contact person.
Note:
The voltage drop at the sine-wave filter can cause an unacceptable temperature rise in the motor.
Voltage drop approximately 10 % of the line voltage.
The voltage drop can be compensated by using a sine-wave filter with a step-up transformer. If this is required, please ask your Siemens contact person.
The cabinet dimensions may increase as a result.
L15 Sine-wave filter integrated in control cabinet or additional cabinet, suitable for motor frequencies ? 60 Hz, voltage drop approx. 10 % of the line voltage
With option L15 a sine-wave filter for motor frequencies of ? 60 Hz is integrated in the control cabinet.
Sine-wave filters should largely suppress the clock-frequency harmonics at the motor terminals to the extent that the voltage approximates a sinusoidal wave. They are implemented as LC networks.
Due to the large voltage drop of a sine-wave filter, it should normally be checked before it is used whether a dv/dt filter would suffice for the application case. To check this, please send the necessary data (cable length, cable type, cable cross-section, number of parallel cables) to your Siemens contact person.
Note:
The voltage drop at the sine-wave filter can cause an unacceptable temperature rise in the motor.
Voltage drop approximately 10 % of the line voltage.
The voltage drop can be compensated by using a sine-wave filter with a step-up transformer. If this is required, please ask your Siemens contact person.
The cabinet dimensions may increase as a result.
L16 Sine-wave filter IP00 for compact unit, suitable for motor frequencies of ? 75 Hz, voltage drop of approx. 5 % of the line voltage (supplied separately packed)
With option L16 a sine-wave filter for motor frequencies of ? 75 Hz is supplied separately packed with the compact unit.
Sine-wave filters should largely suppress the clock-frequency harmonics at the motor terminals to the extent that the voltage approximates a sinusoidal wave. They are implemented as LC networks.
Due to the large voltage drop of a sine-wave filter, it should normally be checked before it is used whether a dv/dt filter would suffice for the application case. To check this, please send the necessary data (cable length, cable type, cable cross-section, number of parallel cables) to your Siemens contact person.
Note:
The voltage drop at the sine-wave filter can cause an unacceptable temperature rise in the motor.
Voltage drop approximately 5 % of the line voltage.
The voltage drop can be compensated by using a sine-wave filter with a step-up transformer. If this is required, please ask your Siemens contact person.
L17 Sine-wave filter integrated in control cabinet or additional cabinet, suitable for motor frequencies ? 75 Hz, voltage drop approx. 5 % of the line voltage
With option L17 a sine-wave filter for compact units and motor frequencies of ? 75 Hz is integrated in the cabinet system.
Sine-wave filters should largely suppress the clock-frequency harmonics at the motor terminals to the extent that the voltage approximates a sinusoidal wave.
Due to the large voltage drop of a sine-wave filter, it should normally be checked before use whether a dv/dt filter would suffice for the application case. To check this, please send the necessary data (cable length, cable type, cable cross-section, number of parallel cables) to your Siemens contact person.
This voltage drop can cause an unacceptable temperature rise in the motor.
Voltage drop approximately 5 % of the line voltage.
The voltage drop can be compensated by using a sine-wave filter with a step-up transformer. If this is required, please ask your Siemens contact person.
L48, L49, L50, L55, N35, N36, Y11 and Y98
Accessories
L48 Grounding socket outlet 230 V, 50 Hz, 10 A, in control cabinet with 30 mA ground-fault circuit interrupter, external incoming supply
L48 Grounding socket outlet (example shown)
Option L48 comprises one 230 V/50 Hz grounding socket outlet in the control cabinet with a 30 mA ground-fault circuit interrupter and 10 A /B miniature circuit breaker, e.g. for notebook (service).
The socket outlet is supplied from an external incoming supply provided by the customer; the terminals are provided in the converter for this.
Note:
If a plug system other than the SCHUKO grounding system is used, e.g. a British or US plug system, please specify this in the order.
L49 Grounding socket outlet 230 V, 50 Hz, 1 A, in control cabinet with 30 mA ground-fault circuit interrupter, supplied internally
Option L49 comprises one 230 V/50 Hz grounding socket outlet in the control cabinet with a 30 mA ground-fault circuit interrupter and 1 A /C miniature circuit breaker, e.g. for notebook (service).
The socket outlet is supplied from an internal control transformer.
If a plug system other than the SCHUKO grounding system is used, e.g. a British or US plug system, please specify this in the order.
L50 Magnetically attached control cabinet light and door contact switch
L50 Control cabinet light (example shown)
The light is fitted with a fluorescent lamp (8 W) without a socket outlet. It is attached using magnets which ensures a high degree of flexibility.
The lamp is switched via a door contact and supplied via an internal control transformer. The light is installed in the control cabinet.
L55 Cabinet heater to protect against condensation and/or operation with supply air temperature of -5 °C or below
L55 Cabinet heater (example shown)
With option L55 cabinet heaters are used with 250 W per control cabinet.
Cabinet heaters are recommended at low ambient temperatures and high levels of humidity to prevent condensation or frost damage. The number of cabinet heaters installed is determined by the number of cabinet sections.
Cabinet heaters should be used above:
- 85 % air humidity. The maximum permissible air humidity in the switchroom is 95 % (condensation is not permitted).
- -5 °C supply air during operation. The minimum ambient temperature for air-cooled converters is 0 °C in the switchroom.
The heater is controlled by a thermostat built into the control cabinet. It is supplied from the installed control voltage transformer or, if required, from an external control voltage supply.
Available as an ETO option:
- Cabinet heaters with increased output for temperatures between -5 ° and -10 °C.
- The cabinet heater is controlled by a hygrostat.
N35 Controlled outgoing feeder for motor heater, voltage 230 V 1 AC, max. 4 kW
This option is used when the driven motor is equipped with a heater that is supplied from the converter. It is important to note that the heater voltage is identical to the control voltage, normally 230 V/50 Hz.
The outgoing feeder can be controlled internally by the converter or externally.
The heater data (voltage/power) of the heater must be included in the order.
N36 Controlled outgoing feeder for external motor fan – external fan voltage for 3 AC. Converter line voltage, max. 4 kW
This option is used when the driven motor is equipped with an external fan motor that is supplied from the converter. It is important to note that the external fan voltage must be identical to the line voltage.
The outgoing feeder can be controlled internally by the converter or externally. The motor data (voltage/current) of the external fan motor must be included in the order.
Y11 Undervoltage release for main switch or circuit breaker; specify coil voltage
With option Y11 an undervoltage release will be installed for a main switch or circuit breaker. The voltage for this release must be specified.
Application examples:
- In combination with options S01 or S02 and the externally backed-up control voltage of the converter, Safety Integrity Level (SIL) 3 according to EN 61508 can be achieved. There is no need for a second main contactor.
Disadvantage:
Automatic reset is not possible, because the main switch or circuit breaker must be reclosed manually.
An externally backed-up control voltage is necessary. - With an undervoltage release, Safety Integrity Level (SIL) 1 can be achieved without a main contactor and without an EMERGENCY OFF relay.
Disadvantage:
Automatic reset is not possible, because the main switch or circuit breaker must be reclosed manually. An externally backed-up control voltage is necessary.
Note:
Please specify the application case in the order.
Y98 Controlled outgoing feeder for auxiliary drive up to max. 4 kW, please specify type of drive, voltage and number of phases
With option Y98 an outgoing feeder is prepared for an auxiliary drive of up to 4 kW. Please specify the voltage and number of phases as well as the type of drive or function description.
The outgoing feeder can be controlled internally by the converter or externally.
Note:
The voltage for the auxiliary drive must be less than or equal to the line voltage.
L72
Braking chopper
L72 Braking chopper integrated into converter (braking resistor is not included and must be ordered separately)
During motor operation the electrical power flow is from the converter to the motor. During generator operation the electrical power flow is from the motor to the converter (braking of rotating masses, active loads).
The standard version of SINAMICS G180 cannot feed energy back into the system. During braking operation kinetic energy can be converted into heat loss. Approx. 10 % of the braking torque is available in the upper speed range. A braking torque up to 50 % can be achieved without a supplementary device in the mid and lower speed range through oversaturation of the motor. The braking chopper accessory allows an external braking resistor to be connected. The braking torque varies in accordance with the converter type and resistance value. The energy generated is converted to heat via the braking transistor in the braking resistor. Any questions regarding braking resistors and the maximum possible braking torque should be addressed to your Siemens contact person.
A thermal model of the braking resistor incorporated into the converter firmware protects the resistor from overload.
L80, L81, L82, L83 and Y80
CALOMAT CK145
L80 CALOMAT CK145
The CALOMAT CK145 for monitoring motors, transformers, etc. with PTC thermistor temperature sensors to DIN 44081, especially explosion-proof motors, is certified to ATEX 95 (Directive 94/9 EC). The requirements of EN 61800?5?1 – Basic requirements for protective separation in electrical equipment – are also fulfilled in the sensor circuit and between the changeover contacts. Destruction of the supervisory control system due to an insulation fault on the PTC thermistor is almost totally prevented.
The CALOMAT in IP20 degree of protection is uniformly 22.5 mm wide and suitable for mounting on a standard rail to DIN EN 50022. The two changeover contacts can be used for disconnecting the system and for outputting alarms to a higher-level control system. The status of the monitoring circuit is signaled by LEDs for Operation (green) and Fault (red). The CK145 also features a LED for sensor break or sensor short-circuit.
The following generally applies:
- CALOMAT thermal motor protection with ATEX certification.
- Directive 94/9/EC, installed in the control cabinet.
- Devices with protective separation to EN 61800?5?1.
- The general health and safety requirements are fulfilled due to compliance with EN 60947?1/EN 60947?5?1/DIN VDE 0660 Part 302 and Part 303/EN 60079?14.
- Sensor circuit: max. 6 PTC thermistors (< 1.5 k?).
- Acknowledgment button on device and remote acknowledgement is possible.
Note:
When CALOMAT devices with a switch-off function are used, a line contactor must be installed on the input side (option S01 or S02) for compliance with ATEX 95 (Directive 94/9 EC).
CALOMAT devices are used in special cases, e.g. identical design to previously supplied equipment, or for evaluating several PTC thermistors. Otherwise, for evaluating PTC thermistors, peripheral board 2 (option G03) or peripheral board 4 (option G05) must be used.
L80 CALOMAT CK145 without storage for motor temperature prewarning
With this option, the motor prewarning temperature limit is monitored using up to 6 PTC thermistors. If the prewarning temperature is exceeded an alarm is output to the converter. The fault is not stored on the CALOMAT and therefore does not require acknowledgement.
L81 CALOMAT CK145 with storage for motor temperature trip
With this option, the motor trip temperature limit is monitored using up to 6 PTC thermistors. If the trip temperature is reached an alarm is output to the converter. The converter switches itself off. The fault is stored on the CALOMAT and therefore has to be acknowledged.
Note:
When CALOMAT devices are used for switch-off, a line contactor must be installed on the input side (option S01 or S02) for compliance with ATEX 95 (Directive 94/9 EC).
L82 CALOMAT CK145 without storage for transformer temperature prewarning
With this option, the transformer prewarning temperature limit is monitored using up to 6 PTC thermistors. If the prewarning temperature is exceeded an alarm is output to the converter. The fault is not stored on the CALOMAT and therefore does not require acknowledgement.
L83 CALOMAT CK145 with storage for transformer temperature trip
With this option, the transformer trip temperature limit is monitored using up to 6 PTC thermistors. If the trip temperature is reached an alarm is output to the converter. The converter switches itself off. The fault is stored on the CALOMAT and therefore has to be acknowledged.
Note:
When CALOMAT devices are used for switch-off, a line contactor must be installed on the input side (option S01 or S02) for compliance with ATEX 95 (Directive 94/9 EC).
Apart from disconnecting the converter, it is also recommended that the already existing tripping device on site is disconnected that is connected upstream of the transformer, such as the medium-voltage switch.
Y80 CALOMAT CK145 for other PTC thermistor temperature monitoring functions
With this option, a temperature limit is monitored using up to 6 PTC thermistors. If the temperature limit is reached an alarm is output to the converter. Please specify whether the fault should be stored on the CALOMAT and therefore has to be acknowledged or not.
L87
Insulation monitoring
L87 Integrated insulation monitoring system for operation on the secondary side of unit transformer in an IT system
L87 Insulation monitoring
An insulation monitor must be used if the converter is connected to a three-winding transformer. The insulation monitor IRDH 275 from Bender monitors the entire galvanically coupled circuit for insulation faults.
This option is included as standard fully wired up in the cabinet for insulation monitoring with 12-pulse and higher-pulse converters on a unit transformer that is not grounded on the secondary side.
Function:
The insulation resistance of all galvanically coupled components (converter transformer secondary winding, cables, converter, motor) is monitored by means of a measured signal that is modulated onto the line supply. If the insulation resistance is undershot, an alarm or trip message is output.
Notice:
Only ONE insulation monitoring device at a time is permitted in the entire galvanically coupled network. False tripping occurs if 2 devices are used. This option is therefore only suitable for converter operation with one converter.
L90, L91, L92, L93, L94, Y90 and Y94
Pt100 evaluation unit
Inadmissible option combinations L90, L92 and L94 as well as L91, L93 and L94
Output filter | L90 | L91 | L92 | L93 | L94 | Y90 | Y94 | |
---|---|---|---|---|---|---|---|---|
Pt100 evaluation unit for motor winding temperature, integrated in control cabinet for monitoring of 3 ? Pt100 or 3 ? KTY83/84 sensors. | L90 | ? | – | ? | – | ? | ? | |
Pt100 evaluation unit for motor bearing temperature, integrated in control cabinet for monitoring of 2 ? Pt100 or 2 ? KTY83/84 sensors. | L91 | ? | ? | – | – | ? | ? | |
Pt100 evaluation unit for motor winding temperature, integrated in control cabinet for monitoring 3 ? Pt100 sensors; plus an analog output 0 to 10 V or 0(4) to 20 mA connected to terminals for the hottest winding temperature. | L92 | – | ? | ? | – | ? | ? | |
Pt100 evaluation unit for motor bearing temperature, integrated in control cabinet for monitoring 2 ? Pt100 sensors or 2 ? KTY83/84 sensors; plus two analog outputs 0 to 10 V or 0(4) to 20 mA connected to terminals for bearing temperature. | L93 | ? | – | ? | – | ? | ? | |
Pt100 evaluation unit for motor winding and bearing temperatures, integrated in control cabinet for monitoring 6 ? Pt100 sensors; plus two analog outputs 0 to 10 V or 0(4) to 20 mA connected to terminals for the hottest winding and bearing temperatures. | L94 | – | – | – | – | ? | ? | |
Pt100 evaluation unit for other temperature monitoring functions, integrated in control cabinet for monitoring of 3 ? Pt100 or 3 ? KTY83/84 sensors. | Y90 | ? | ? | ? | ? | ? | ? | |
Pt100 evaluation unit for other temperature monitoring functions, integrated in control cabinet for monitoring 6 ? Pt100 sensors; plus two analog outputs 0 to 10 V or 0(4) to 20 mA connected to terminals. | Y94 | ? | ? | ? | ? | ? | ? |
? | Options are combinable. |
– | Options mutually exclude each other. |
L90 Pt100 evaluation unit for motor winding temperature, integrated in control cabinet for monitoring of 3 ? Pt100 or 3 ? KTY83/84 sensors
L90 Siemens 3RS1041-1GW50
Pt100 evaluation unit for motor winding temperature, integrated for 3 ? Pt100/1000 or 3 ? KTY83/84 sensors with temperature indication on evaluation unit, alarm and trip message on converter display or integrated into the group warning or group fault.
Note:
Please specify alarm and trip limits in the order for motors that are not included in the scope of supply.
L91 Pt100 evaluation unit for motor bearing temperature, integrated in control cabinet for monitoring of 2 ? Pt100 or 2 ? KTY83/84 sensors
Pt100 evaluation unit for motor bearing temperature, integrated in control cabinet for 2 ? Pt100/1000 or 2 ? KTY83/84 sensors; temperature indication on evaluation unit, alarm and trip message on converter display or integrated into the group warning or group fault.
Note:
Please specify alarm and trip limits in the order for motors that are not included in the scope of supply.
L92 Pt100 evaluation unit for motor winding temperature, integrated in control cabinet for monitoring 3 ? Pt100 sensors; plus an analog output 0 to 10 V or 0(4) to 20 mA connected to terminals for the hottest winding temperature
L92 Pt100 Ziehl TR400
Pt100 evaluation unit for 3 x Pt100 sensors for 3 winding sensors (1 reserve), installed in the control cabinet. With temperature indication on the evaluation unit; alarm and trip message on the converter display or integrated in the group warning or group fault.
Also one analog output 0 to 10 V or 0(4) to 20 mA for the hottest winding temperature for further processing, e.g. in the main control system; applied to terminals.
Note:
Please specify alarm and trip limits in the order for motors that are not included in the scope of supply.
L93 Pt100 evaluation unit for motor bearing temperature, integrated in control cabinet for monitoring 2 ? Pt100 sensors or 2 ? KTY83/84 sensors; plus two analog outputs 0 to 10 V or 0(4) to 20 mA connected to terminals for bearing temperature
Pt100 evaluation unit for 2 x Pt100 sensors or 2 x KTY83/84 sensors for motor bearing temperature, integrated in the control cabinet. With temperature indication on the evaluation unit; alarm and trip message on the converter display or integrated in the group warning or group fault.
Also two analog outputs 0 to 10 V or 0(4) to 20 mA for the bearing temperature for further processing, e.g. in the main control system; applied to terminals.
Note:
Please specify alarm and trip limits in the order for motors that are not included in the scope of supply.
L94 Pt100 evaluation unit for motor winding and bearing temperatures, integrated in control cabinet for monitoring 6 ? Pt100 sensors; plus two analog outputs 0 to 10 V or 0(4) to 20 mA connected to terminals for the hottest winding and bearing temperatures
L94 Pt100 Ziehl TR600
Pt100 evaluation unit for 6 x Pt100 sensors for 3 winding sensors and 2 bearing sensors (1 reserve), integrated in the control cabinet; temperature indication on evaluation unit; alarm and trip message on converter display or integrated into the group warning or group fault.
Also one analog output 0 to 10 V or 0(4) to 20 mA for the hottest winding temperature and one analog output 0 to 10 V or 0(4) to 20 mA for the hottest bearing temperature for further processing, e.g. in the main control system; applied to terminals.
Note:
Please specify alarm and trip limits in the order for motors that are not included in the scope of supply.
Y90 Pt100 evaluation unit for other temperature monitoring functions, integrated in control cabinet for monitoring of 3 ? Pt100 or 3 ? KTY83/84 sensors
For image, see option L90 Siemens 3RS1041-1GW50.
Pt100 evaluation unit for motor winding temperature, integrated in control cabinet for 3 ? Pt100/1000 or 3 ? KTY83/84 sensors; temperature indication on evaluation unit, alarm and trip message on converter display or integrated into the group warning or group fault.
Note:
Please specify alarm and trip limits or which temperatures should be monitored in the order.
Y94 Pt100 evaluation unit for other temperature monitoring functions, integrated in control cabinet for monitoring 6 ? Pt100 sensors; plus two analog outputs 0 to 10 V or 0(4) to 20 mA connected to terminals
For image, see option L94 Pt100 Ziehl TR600.
Pt100 evaluation unit for 6 x Pt100 sensors integrated in control cabinet; temperature indication on evaluation unit; alarm and trip message on converter display or integrated into the group warning or group fault.
Also two analog outputs 0 to 10 V or 0(4) to 20 mA applied to terminals.
Note:
Please specify alarm and trip limits or which temperatures should be monitored in the order.
M05, M06, M07, M13, M17, M19, M24, M28, M34, M38, M39, M40, M59, M78, Y09 and Y19
Cabinet options
M05 Control cabinet base, welded and suitable for use with transport rollers in RAL 7022, height 200 mm
M05 Control cabinet base, welded
The control cabinet base allows larger bending radii for cables (cable inlet from below) and enables them to be routed within the control cabinet base.
The control cabinet base is welded and suitable for use with transport rollers. The standard color is RAL 7022; a special paint finish for the control cabinet base is not possible. It is delivered completely assembled with the cabinet.
Base element 200 mm painted (RAL 7022).
Note:
The control cabinet base is supplied fully assembled with the converter cabinet.
M06 Control cabinet base RAL 7022/9005 as standard, height 100 mm
M06 Control cabinet base
The control cabinet base allows larger bending radii for cables (cable inlet from below) and enables them to be routed within the control cabinet base.
The standard color is RAL 7022/9005; a special paint finish for the control cabinet base is not possible. The height is 100 mm.
Note:
For transport reasons, the control cabinet bases are delivered separately or packed alongside the cabinet and must be mounted on site before the cabinet is assembled.
M07 Control cabinet base RAL 7022/9005 as standard, height 200 mm
For image, see option M06 Control cabinet base.
The control cabinet base allows larger bending radii for cables (cable inlet from below) and enables them to be routed within the control cabinet base.
The standard color is RAL 7022/9005; a special paint finish for the control cabinet base is not possible. The height is 200 mm.
Note:
For transport reasons, the control cabinet bases are delivered separately or packed alongside the cabinet and must be mounted on site before the cabinet is assembled.
M13 Cable entry from the top: power cable
With option M13 the cables for mains connection will enter the control cabinet from the top.
The width of the cabinet may increase depending on the converter type and equipment. Please contact the factory regarding the exact dimensions of the converter with this option.
M34 Cable entry from the top: control cables
With option M34 the cables for the control cables will enter the cabinet from the top.
The width of the cabinet may increase depending on the converter type and equipment. Please contact the factory regarding the exact dimensions of the converter with this option.
M78 Cable entry from the top: motor cables
With option M78 the motor cables will enter the control cabinet from the top.
The width of the cabinet may increase depending on the converter type and equipment. Please contact the factory regarding the exact dimensions of the converter with this option.
M17 Door opening angle 180°
M17 Door opening angle 180°
With option M17 all standard hinges are replaced with 180° hinges. The converter cabinet door can therefore normally open 180°, but the opening angle may be reduced by components installed in the control cabinet door.
M19 Window in door for viewing internal display
M19 Example of window in door for viewing internal display
With this option, an inspection window is installed in the control cabinet door. The internal converter display can be read through this.
M24 Partitions between compact units for cabinet systems
M24 Partitions between the compact units (example shown)
Partitions can be used between compact units in cabinet systems to implement clear separation of the converter with the associated controller.
M28 Door hinge on left
M28 Door hinge on left
The SINAMICS G180 converter is supplied as standard up to a cabinet width of 800 mm with the door hinged on the right (hinges on right). With this option, the doors are hinged on the left (hinges on left).
Note:
This option is not possible in the case of double doors (cabinet width 1000 mm or 1200 mm).
M38 Comfort-grip handle with double-bit key lock
M38 Comfort-grip handle with double-bit key lock (example shown)
It is unlocked using a standard double-bit key. The unlocked handle unfolds forwards and is lifted to open the lock.
- Material: die-cast zinc
- Surface: powder-coated
- Standard version in RAL 7035
M39 Comfort-grip handle with integrated pushbutton
M39 Comfort-grip handle with integrated pushbutton (example shown)
It is unlocked using a pushbutton insert. The unlocked handle unfolds forwards and is lifted to open the lock. The cabinet door can then be opened easily without the need for additional tools.
- Material: die-cast zinc
- Surface: powder-coated
- Standard version in RAL 7035
M40 Comfort-grip handle with cylinder lock
M40 Comfort-grip handle with cylinder lock (example shown)
A safety insert is used for unlocking, lock No. 3514 E with 2 keys. The unlocked handle unfolds forwards and is lifted to open the lock.
- Material: die-cast zinc
- Surface: powder-coated
- Standard version in RAL 7035
M59 Air supply via cable floor (no need for filter elements in the door)
If the converter cabinet is erected on a false floor or duct which forms part of a forced ventilation system, the converter can be ordered with closed cabinet doors. To ensure an adequate air inlet cross-section, the units are shipped without the standard base plates. In this case, the customer must ensure that no dirt/dust or moisture can enter the converter. Cables must not be routed in such a way that they impede the flow of air through the cabinet floor opening. If the area beneath the converter can be accessed, the customer must provide touch protection.
Y09 Special control cabinet paint color: Please specify RAL
Y09 Example special paint
As standard, the converter cabinet units are delivered in RAL 7035. The special paint finish must be stated in plain text in the order. All RAL colors which are available as powder coatings can be selected. This may extend the delivery time.
Important:
The protective top cover for IP21 and the protective top cover in option M43 is supplied in RAL 7035 as standard, but it can also be painted in the special paint of the cabinet Y09. This must be specified in the order in which case the delivery time may be extended. If a special color is requested for the cabinet (Order code Y09), the top cover in option M54 is also painted in this color. The molded plastic parts (e.g. ventilation grilles) are colored RAL 7035 and cannot be painted.
Y19 Window in door for viewing internal components
Y19 Example of window in door for viewing internal components
With this option, an inspection window is installed in the control cabinet door. An internal component can be read through this.
M21, M41, M43, M54, M55 and M63
Degrees of protection
The EN 60529 standard covers the protection of electrical equipment by means of housings, covers or equivalent, and includes:
- Protection of persons against accidental contact with live or moving parts within the housing and protection of the equipment against the ingress of solid foreign matter (touch protection and protection against ingress of solid foreign matter)
- Protection of the equipment against the ingress of water (water protection)
- Abbreviations for the internationally agreed degrees of protection
The degrees of protection are specified by abbreviations comprising the code letters IP and two digits.
Degree of protection | First digit | Second digit |
---|---|---|
IP20
| Protected against solid foreign matter, diameter ? 12.5 mm | No water protection |
IP21
| Protected against solid foreign matter, diameter ? 12.5 mm | Protected against drip water Vertically falling water drops shall not have a harmful effect. |
IP41 Option M41 for cabinet units and systems | Protected against solid foreign matter, diameter ? 1 mm | Protected against drip water Vertically falling water drops shall not have a harmful effect. |
IP43 Option M43 for cabinet units and systems | Protected against solid foreign matter, diameter ? 1 mm | Protected against spray water Water sprayed on both sides of the vertical at an angle of up to 60° shall not have a harmful effect. |
IP54 Option M54 for cabinet units (standard for liquid-cooled cabinet units) | Protected against dust Ingress of dust is not totally prevented, but dust must not be allowed to enter in such quantities that the functioning or safety of the equipment is impaired. | Protected against splash water Water splashing onto the enclosure from any direction shall not have a harmful effect. |
IP55 Option M55 for cabinet units | Protected against dust Ingress of dust is not totally prevented, but dust must not be allowed to enter in such quantities that the functioning or safety of the equipment is impaired. | Protected against jet-water Water splashing onto the enclosure from any direction (nozzle) shall not have a harmful effect. |
The devices are intended for indoor installation and are suitable for climatic environmental conditions of Class 3K3 according to EN 60721, higher requirements fulfilled on request.
Note:
For transport reasons, the top covers are delivered separately and must be fitted on site.
The protective top cover for IP21 and the protective top cover in option M43 is supplied in RAL 7035 as standard, but it can also be painted in the special paint of the cabinet Y09 . This must be specified in the order in which case the delivery time may be extended. If a special color is requested for the cabinet (Order code Y09), the top cover in option M54 is also painted in this color. The molded plastic parts (e.g. ventilation grilles) are colored RAL 7035 and cannot be painted.
M21 Increased degree of protection IP21 for compact units
With option M21 a protective top cover is supplied separately packed for the compact units. The top cover is 5 mm wider on both sides than the converter. This clearance must be taken into account when installing side-by-side. The air discharge area must be left clear at the front.
M41 Increased degree of protection IP41 for air-cooled cabinet units and systems
M41 Fine-mesh wire grid (example shown)
With option M41 the filter fan or outlet filter is covered with a fine-mesh wire grid in addition to the IP21 top cover.
M43 Increased degree of protection IP43 for air-cooled cabinet units and systems
M43 IP43 top cover (example shown)
With option M43 IP43 degree of protection is achieved using the following combination:
- Top cover IPX3 + fine-mesh wire grid in the filter fan or outlet filter
M54 Increased degree of protection IP54 for air-cooled cabinet units and systems (not suitable for outdoor applications)
M54 Labyrinth top cover (example shown)
With option M54 IP54 degree of protection is achieved using the following combination:
- Labyrinth top cover + filter mat (open-cell polyurethane foam) in filter fan or outlet filter
- With option M63 (air flange for connection to customer's exhaust air systems; air outlet IP00) + filter mat (open-cell polyurethane foam) in filter fan or outlet filter
- Standard degree of protection for liquid-cooled cabinet units
M55 Increased degree of protection IP55 for liquid-cooled cabinet units (no display in cabinet door)
IP55 degree of protection is achieved with option M55 by omitting the converter operator panel or other built-in components with a low degree of protection in the cabinet door in the case of liquid-cooled converters. Additional measures are not required.
M63 Air flange for connection to customer's exhaust air systems (air outlet IP00)
M63 Air flange (example shown)
With option M63 an air flange is provided on the converter. This allows the SINAMICS G180 to be connected to an external exhaust air system so that IP54 degree of protection is achieved.
Important:
For transport reasons, the air flanges are delivered separately and must be fitted on site.
M20 and N50
Wiring options
M20 Minimum cross-section of the internal cabinet wiring 1.5 mm2
With option M20 the internal wiring of the controller in the converter is implemented using a minimum conductor cross-section of 1.5 mm2. Individual electronics leads, such as flat ribbon cables are excluded from this.
N50 Use of halogen-free cables inside cabinet
With option N50 halogen-free cables are used. Individual electronics leads, such as flat ribbon cables are excluded from this.
Q80, Q81, Q82, Q83, Q84 and Q85
Extension of the liability for defects
Option | Description |
---|---|
Q80 | Extension of the liability for defects by 12 months as of commissioning date or by 24 months as of delivery date |
Q81 | Extension of the liability for defects by 18 months as of commissioning date or by 30 months as of delivery date |
Q82 | Extension of the liability for defects by 24 months as of commissioning date or by 36 months as of delivery date |
Q83 | Extension of the liability for defects by 30 months as of commissioning date or by 42 months as of delivery date |
Q84 | Extension of the liability for defects by 36 months as of commissioning date or by 48 months as of delivery date |
Q85 | Extension of the liability for defects by 48 months as of commissioning date or by 60 months as of delivery date |
Conditions for an extension of the liability for defects:
- For all extension periods of liability for defects, for new and subsequent orders, the final destination of the product must be known. The EUNA process is available to obtain this information at http://www.siemens.com/euna, which must be performed by your local Siemens contact person.
- For all 4 and 5 year extension periods of the liability for defects (Q84, Q85), this is only possible in conjunction with a corresponding maintenance contract with regular inspections. This maintenance contract must be signed and concluded with the responsible service department. This must be documented using the EUNA procedure at http://www.siemens.com/euna, which must be performed by your local Siemens contact person.
- The general storage conditions described in the operating instructions must be adhered to, especially the specifications for long-term storage.
- Commissioning must be performed by appropriately qualified personnel. When making liability for defect claims, under certain circumstances, it may be necessary to submit the commissioning report to the department making the decision.
- Periodic maintenance must be performed in accordance with the specifications of the operating instructions. When making liability for defect claims, under certain circumstances, it may be necessary to submit the corresponding maintenance documentation and history.
- The operating conditions correspond to the specifications in the operating instructions, the installation instructions or specific conditions laid down in the contract.
- The extended liability for defects excludes wearing parts such as fans or filters. This does not apply if it can be clearly proven that the failure is a premature one.
- Otherwise, the general conditions regarding liability for defects apply as agreed in the delivery contract.
S01, S02, S03, S04, S06, S08, S09, S11, S12, S21, S22, S23, S24, S31, S32, S41 and G08
Standard accessories packages
Standard accessories packages | Option | ||||||||||||||
---|---|---|---|---|---|---|---|---|---|---|---|---|---|---|---|
Accessories package S01 with main switch, line contactor, EMERGENCY OFF pushbutton and safety relay, board G03, local/remote switch |
|
|
|
|
|
|
|
|
|
| S01 | ||||
Accessories package S02 with circuit breaker, line contactor, EMERGENCY OFF pushbutton and safety relay, board G03, local/remote switch |
|
|
|
|
|
|
|
|
| S02 |
| ||||
Accessories package with main switch, line contactor, board G03, local/remote switch | S03 | ||||||||||||||
Accessories package with circuit breaker, line contactor, board G03, local/remote switch | S04 | ||||||||||||||
Accessories package with main switch, line contactor, Calomat, RCU box connection | S06 | ||||||||||||||
Bypass for smooth line synchronization (soft start function) incl. line-side main switch and contactors at the converter output and in bypass |
|
|
|
|
|
|
|
| S08 |
|
| ||||
Bypass for smooth line synchronization (soft start function) incl. line-side circuit breaker and contactors at the converter output and in bypass |
|
|
|
|
|
|
| S09 |
|
|
| ||||
Accessories package S11 with line-side main switch, board G03, local/remote switch |
|
|
|
|
|
| S11 |
|
|
|
| ||||
Accessories package S12 with line-side circuit breaker, board G03, local/remote switch |
|
|
|
|
| S12 |
|
|
|
|
| ||||
Bypass with line-side main switch, contactors at converter output and in bypass, switchover between manual and automatic, local/remote switch |
|
|
|
| S21 |
|
|
|
|
|
| ||||
Bypass with line-side circuit breaker, contactors at converter output and in bypass, switchover between manual and automatic, local/remote switch |
|
|
| S22 |
|
|
|
|
|
|
| ||||
Bypass with line-side main switch, contactors at converter output and in bypass, EMERGENCY OFF safety relay, switchover between manual and automatic, local/remote switch |
|
| S23 |
|
|
|
|
|
|
|
| ||||
Bypass with line-side circuit breaker, contactors at converter output and in bypass, EMERGENCY OFF safety relay, switchover between manual and automatic, local/remote switch |
| S24 |
|
|
|
|
|
|
|
|
| ||||
NAMUR accessories package with Test/Normal operation switch, option G05, terminal strip compliant with NAMUR NE37 (without main switch) | S31 |
|
|
|
|
|
|
|
|
|
| ||||
NAMUR accessories package with Test/Normal operation switch, main switch, line contactor, option G05, terminal strip compliant with NAMUR NE37 | S32 | ||||||||||||||
Option description | |||||||||||||||
4-line display in the door | ? | ? | ? | ? | ? | ? | ? | ? | ? | ? | ? | ? | ? | ? | ? |
Main switch as switch disconnector incl. lockable door handle (for input current > 125 A also with short-circuit release) | ? |
|
| ? |
| ? |
| ? |
| ? | ? | ? |
| ? | |
Circuit breaker with adjustable overcurrent release and short-circuit release incl. lockable door handle |
| ? |
| ? |
| ? |
| ? |
| ? | ? |
| |||
Main contactor on input for safety-related line disconnection | ? |
|
|
|
|
|
|
|
|
| ? | ? | ? | ? | ? |
EMERGENCY OFF safety relay according to EN ISO 13849?1 or SIL 11) according to EN 61508 | ? |
| ? | ? |
|
|
|
|
|
| ? | ? | |||
EMERGENCY OFF pushbutton and EMERGENCY OFF reset in the cabinet door | ? |
| ? | ? |
|
|
|
|
|
| ? | ? | |||
Selector switch for local/remote operation in the cabinet door |
| ? | ? | ? | ? | ? | ? | ? | ? | ? | ? | ? | ? | ||
Output-side converter contactor |
| ? | ? | ? | ? |
|
| ? | ? |
|
| ||||
Bypass contactor |
| ? | ? | ? | ? |
|
| ? | ? |
|
| ||||
Hardware for line voltage measurement and synchronizer via the converter |
|
|
|
|
|
|
| ? | ? |
|
| ||||
Input-side disconnection possibility for the converter | ? |
| ? | ? | ? | ? |
|
|
|
| ? | ? | ? |
|
|
Motor monitoring also in bypass mode |
| ? | ? | ? | ? |
|
|
|
|
|
| ||||
Manual or automatic bypass switchover |
| ? | ? | ? | ? |
|
|
|
|
|
| ||||
Button "Bypass On" with lamp "Bypass On" |
| ? | ? | ? | ? |
|
|
|
|
|
| ||||
Button "Bypass Off" |
| ? | ? | ? | ? |
|
|
|
|
|
| ||||
Button "Reset motor fault" with lamp "Motor fault" |
| ? | ? | ? | ? |
|
|
|
|
|
| ||||
Terminal strip in accordance with NAMUR recommendation NE37 | ? | ? |
|
|
|
|
|
|
|
|
|
| |||
Selector switch for Test/Normal operation in the cabinet | ? | ? |
|
|
|
|
|
|
|
|
|
| |||
Peripheral board 2 (G03) incl. ATEX-certified PTC input (G03) |
|
|
|
|
| ? | ? | ? | ? | ? | ? | ? | ? | ||
Peripheral board 4 (G05) incl. automatic supply disconnection, executed in accordance with EN ISO 13849?1 up to Cat. 3 and ATEX-certified PTC input | ? | ? |
|
|
|
|
|
|
|
|
|
|
1) SIL 2 available with option G08, SIL 3 on request.
S41 Main switch integrated into compact unit (might alter dimensions of unit)
With option S41 compact units can be optionally fitted with a main switch as a switch disconnector. The handle can be operated and locked from the outside.
G08 Peripheral board 4 (G05) instead of peripheral board 2 (G03) (only in combination with package S01, S02, S03, S04, S08, S09, S11, S12)
T01 and Y33
Label for plant identification
T01 Example of a label
T01 Cabinet designation TAG/ITEM number according to ordering data
Resopal labels (white with black lettering) for identifying the converter are available. The labels are screwed onto the cabinet door. Please specify the TAG/ITEM number in the order.
Dimensions 450 ? 300 mm max.
Y33 Customized labels
The converter cabinets are labeled with customer-specific text (e.g. "Pump No. 1").
The text and number of labels must be specified in plain text. The labels are supplied as standard in Resopal with black lettering on a white background. The labels are screwed onto the cabinet door.
Dimensions 450 ? 300 mm max.
T23, T24, T25, T26, T58, T60, T74, T76, T82, T85 and T86
Converter display language (language 1/language 2)
Different languages are available for the 4-line converter display of the SINAMICS G180. Two languages can be parameterized via the IMS. The language is switched on the display under the menu item "P-EXTRAS/Language" or by pressing down the button S for 2 seconds.
T74 Example: German display/T76 English display
Option | Description |
---|---|
T23 | Display language Norwegian/English |
T24 | Display language Swedish/English |
T25 | Display language Czech/English |
T26 | Display language Hungarian/English |
T58 | Display language French/English |
T60 | Display language Spanish/English |
T74 | Display language German/English |
T76 | Display language English/German |
T82 | Display language Portuguese/English |
T85 | Display language Russian/English |
T86 | Display language Polish/English |
U04
Gost-R certificate
With option U04 a converter design is supplied with Gost conformity.
A Gost-R certificate is not generally required for frequency converters. A Gost-R negative certificate is issued as standard for a SINAMICS G180 to be exported to Russia. This confirms that the product is not subject to mandatory Gost-R certification.
Voluntary certification (Gost-R certificate) is, however, recommended for the following reasons:
- It simplifies customs clearance
- Certification on a voluntary basis increases the sales opportunities on the Russian market, because the consumer trusts certified goods.
- Voluntary certification is required in some cases on the Russian market (in retail, construction industry, etc.).
- Accredited certification bodies guarantee, with their signatures, conformity of the certified goods with Russian standards.
- An attested and signed copy of the Gost-R certificate must be presented for every delivery to the Russian federation for customs clearance. It is also required for subsequent sales/marketing within the country.
H80, H81, H82, H83, H84, H85 and H86
Cabinet widths for cabinet systems with compact units
Option | Description |
---|---|
H80 | Cabinet width: 406 mm |
H81 | Cabinet width: 606 mm |
H82 | Cabinet width: 806 mm |
H83 | Cabinet width: 1006 mm |
H84 | Cabinet width: 1206 mm |
H85 | Cabinet width: 1406 mm |
H86 | Cabinet width: 1606 mm |
H90, H91, H92, H93 and H94
Additional cabinets for cabinet units
Option | Description |
---|---|
H90 | Additional cabinet: 400 mm |
H91 | Additional cabinet: 600 mm |
H92 | Additional cabinet: 800 mm |
H93 | Additional cabinet: 1000 mm |
H94 | Additional cabinet: 1200 mm |
V61, V62 and V63
Ambient temperature for air-cooled converters
The maximum permissible coolant temperature is 40 °C for air-cooled units. If operation is required with higher coolant temperatures, derating is necessary.
Option | Description |
---|---|
V61 | 45 °C ambient temperature (with corresponding derating) |
V62 | 50 °C ambient temperature (with corresponding derating) |
V63 | 55 °C ambient temperature (for compact units with corresponding derating) |
V66, V67 and V68
Water inlet temperature for liquid-cooled converters
The maximum permissible water inlet temperature is between 28 and 35 °C depending on the converter type (see technical data for maximum cooling water temperature). If operation is required with higher coolant temperatures, derating is necessary.
Option | Description |
---|---|
V66 | 30 °C water inlet temperature (with corresponding derating) |
V67 | 35 °C water inlet temperature (with corresponding derating) |
V68 | 40 °C water inlet temperature (with corresponding derating) |
V86, V87, V88 and V89
Installation altitude
At an installation altitude for the SINAMICS G180 of over 1000 m above sea level, reduced cooling caused by the lower air pressure and cosmic radiation means that the input voltage must be reduced (see the section "Characteristic curves" under "Configuring instructions"). Options V86 to V89 specify the installation altitude of the converter.
Option | Description |
---|---|
V86 | Installation altitude max. 1500 m above sea level (with corresponding derating) |
V87 | Installation altitude max. 2000 m above sea level (with corresponding derating) |
V88 | Installation altitude max. 2500 m above sea level (with corresponding derating) |
V89 | Installation altitude max. 3000 m above sea level (with corresponding derating) |
V70, V71, V72, V73, V74, V75, V76, V77, V78, V79, V80 and Y70
Line voltages
Options V70 to Y70 are used to select the line voltage. These options mutually exclude each other.
Option | Description |
---|---|
V70 | Line voltage 380 V, 50 Hz |
V71 | Line voltage 400 V, 50 Hz |
V72 | Line voltage 415 V, 50 Hz |
V73 | Line voltage 500 V, 50 Hz |
V74 | Line voltage 660 V, 50 Hz |
V75 | Line voltage 690 V, 50 Hz |
V76 | Line voltage 440 V, 60 Hz |
V77 | Line voltage 460 V, 60 Hz |
V78 | Line voltage 480 V, 60 Hz |
V79 | Line voltage 600 V, 60 Hz |
V80 | Line voltage 660 V, 60 Hz |
Y70 | Special line voltage; please specify voltage |
Y13
Language of manual
Y13 Different languages for manual
The following languages are available for the manual:
- Bulgarian
- Czech
- German
- English
- Spanish
- French
- Dutch
- Polish
- Russian
- Norwegian
Note:
Other languages on request.
Deprecated: Function eregi() is deprecated in /home/h101150-2/siemens71.ru/docs/kip/kip.php on line 23
Deprecated: Function eregi() is deprecated in /home/h101150-2/siemens71.ru/docs/kip/kip.php on line 23
Deprecated: Function eregi() is deprecated in /home/h101150-2/siemens71.ru/docs/kip/kip.php on line 30
Deprecated: Function eregi() is deprecated in /home/h101150-2/siemens71.ru/docs/kip/kip.php on line 30
Deprecated: Function eregi() is deprecated in /home/h101150-2/siemens71.ru/docs/kip/kip.php on line 30
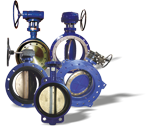
Deprecated: Function eregi() is deprecated in /home/h101150-2/siemens71.ru/docs/kip/kip.php on line 30
Deprecated: Function eregi() is deprecated in /home/h101150-2/siemens71.ru/docs/kip/kip.php on line 30
Àðìàòóðà DENDOR
Deprecated: Function eregi() is deprecated in /home/h101150-2/siemens71.ru/docs/kip/kip.php on line 23
Deprecated: Function eregi() is deprecated in /home/h101150-2/siemens71.ru/docs/kip/kip.php on line 30
Deprecated: Function eregi() is deprecated in /home/h101150-2/siemens71.ru/docs/kip/kip.php on line 30
Deprecated: Function eregi() is deprecated in /home/h101150-2/siemens71.ru/docs/kip/kip.php on line 30
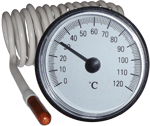
Deprecated: Function eregi() is deprecated in /home/h101150-2/siemens71.ru/docs/kip/kip.php on line 30
Deprecated: Function eregi() is deprecated in /home/h101150-2/siemens71.ru/docs/kip/kip.php on line 30
Äàò÷èêè è èçìåðèòåëè
Deprecated: Function eregi() is deprecated in /home/h101150-2/siemens71.ru/docs/kip/kip.php on line 23
Deprecated: Function eregi() is deprecated in /home/h101150-2/siemens71.ru/docs/kip/kip.php on line 30
Deprecated: Function eregi() is deprecated in /home/h101150-2/siemens71.ru/docs/kip/kip.php on line 30
Deprecated: Function eregi() is deprecated in /home/h101150-2/siemens71.ru/docs/kip/kip.php on line 30
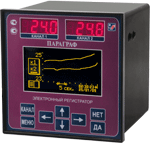
Deprecated: Function eregi() is deprecated in /home/h101150-2/siemens71.ru/docs/kip/kip.php on line 30
Deprecated: Function eregi() is deprecated in /home/h101150-2/siemens71.ru/docs/kip/kip.php on line 30
Ðåãóëÿòîðû è ðåãèñòðàòîðû
Deprecated: Function eregi() is deprecated in /home/h101150-2/siemens71.ru/docs/kip/kip.php on line 23
Deprecated: Function eregi() is deprecated in /home/h101150-2/siemens71.ru/docs/kip/kip.php on line 30
Deprecated: Function eregi() is deprecated in /home/h101150-2/siemens71.ru/docs/kip/kip.php on line 30
Deprecated: Function eregi() is deprecated in /home/h101150-2/siemens71.ru/docs/kip/kip.php on line 30
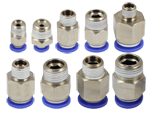
Deprecated: Function eregi() is deprecated in /home/h101150-2/siemens71.ru/docs/kip/kip.php on line 30
Deprecated: Function eregi() is deprecated in /home/h101150-2/siemens71.ru/docs/kip/kip.php on line 30
Ïíåâìàòè÷åñêîå îáîðóäîâàíèå
Deprecated: Function eregi() is deprecated in /home/h101150-2/siemens71.ru/docs/kip/kip.php on line 23
Deprecated: Function eregi() is deprecated in /home/h101150-2/siemens71.ru/docs/kip/kip.php on line 30
Deprecated: Function eregi() is deprecated in /home/h101150-2/siemens71.ru/docs/kip/kip.php on line 30
Deprecated: Function eregi() is deprecated in /home/h101150-2/siemens71.ru/docs/kip/kip.php on line 30
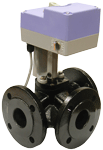
Deprecated: Function eregi() is deprecated in /home/h101150-2/siemens71.ru/docs/kip/kip.php on line 30
Deprecated: Function eregi() is deprecated in /home/h101150-2/siemens71.ru/docs/kip/kip.php on line 30
Êðàíû è Êëàïàíû
Deprecated: Function eregi() is deprecated in /home/h101150-2/siemens71.ru/docs/kip/kip.php on line 23
Deprecated: Function eregi() is deprecated in /home/h101150-2/siemens71.ru/docs/kip/kip.php on line 30
Deprecated: Function eregi() is deprecated in /home/h101150-2/siemens71.ru/docs/kip/kip.php on line 30
Deprecated: Function eregi() is deprecated in /home/h101150-2/siemens71.ru/docs/kip/kip.php on line 30
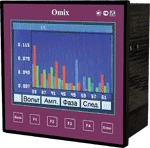
Deprecated: Function eregi() is deprecated in /home/h101150-2/siemens71.ru/docs/kip/kip.php on line 30
Deprecated: Function eregi() is deprecated in /home/h101150-2/siemens71.ru/docs/kip/kip.php on line 30
Èçìåðèòåëüíûå ïðèáîðû
Deprecated: Function eregi() is deprecated in /home/h101150-2/siemens71.ru/docs/kip/kip.php on line 23
Deprecated: Function eregi() is deprecated in /home/h101150-2/siemens71.ru/docs/kip/kip.php on line 30
Deprecated: Function eregi() is deprecated in /home/h101150-2/siemens71.ru/docs/kip/kip.php on line 30
Deprecated: Function eregi() is deprecated in /home/h101150-2/siemens71.ru/docs/kip/kip.php on line 30
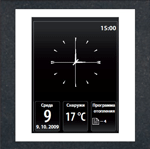
Deprecated: Function eregi() is deprecated in /home/h101150-2/siemens71.ru/docs/kip/kip.php on line 30
Deprecated: Function eregi() is deprecated in /home/h101150-2/siemens71.ru/docs/kip/kip.php on line 30
Ñèñòåìû áåñïðîâîäíîãî óïðàâëåíèÿ «óìíûé äîì»
Deprecated: Function eregi() is deprecated in /home/h101150-2/siemens71.ru/docs/kip/kip.php on line 23
Deprecated: Function eregi() is deprecated in /home/h101150-2/siemens71.ru/docs/kip/kip.php on line 30
Deprecated: Function eregi() is deprecated in /home/h101150-2/siemens71.ru/docs/kip/kip.php on line 30
Deprecated: Function eregi() is deprecated in /home/h101150-2/siemens71.ru/docs/kip/kip.php on line 30
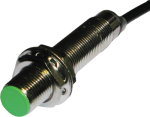
Deprecated: Function eregi() is deprecated in /home/h101150-2/siemens71.ru/docs/kip/kip.php on line 30
Deprecated: Function eregi() is deprecated in /home/h101150-2/siemens71.ru/docs/kip/kip.php on line 30
Áåñêîíòàêòíûå âûêëþ÷àòåëè Êîíå÷íûå âûêëþ÷àòåëè Îïòè÷åñêèå äàò÷èêè Ýíêîäåðû
Deprecated: Function eregi() is deprecated in /home/h101150-2/siemens71.ru/docs/kip/kip.php on line 23
Deprecated: Function eregi() is deprecated in /home/h101150-2/siemens71.ru/docs/kip/kip.php on line 30
Deprecated: Function eregi() is deprecated in /home/h101150-2/siemens71.ru/docs/kip/kip.php on line 30
Deprecated: Function eregi() is deprecated in /home/h101150-2/siemens71.ru/docs/kip/kip.php on line 30
Deprecated: Function eregi() is deprecated in /home/h101150-2/siemens71.ru/docs/kip/kip.php on line 30

Deprecated: Function eregi() is deprecated in /home/h101150-2/siemens71.ru/docs/kip/kip.php on line 30
SKW-FS - Óñòàíîâêà óìÿã÷åíèÿ
Deprecated: Function eregi() is deprecated in /home/h101150-2/siemens71.ru/docs/kip/kip.php on line 23
Deprecated: Function eregi() is deprecated in /home/h101150-2/siemens71.ru/docs/kip/kip.php on line 30
Deprecated: Function eregi() is deprecated in /home/h101150-2/siemens71.ru/docs/kip/kip.php on line 30
Deprecated: Function eregi() is deprecated in /home/h101150-2/siemens71.ru/docs/kip/kip.php on line 30
Deprecated: Function eregi() is deprecated in /home/h101150-2/siemens71.ru/docs/kip/kip.php on line 30
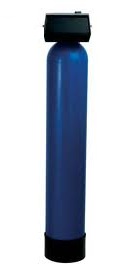
Deprecated: Function eregi() is deprecated in /home/h101150-2/siemens71.ru/docs/kip/kip.php on line 30
SKW-FK - Óñòàíîâêà îáåçæåëåçèâàíèÿ