| |
?
Use of Series 6 in hazardous areas
Dependent on the application, the measuring equipment can include the following parts:
- Analyzer
- EEx p safety equipment (purging unit)
- Flame arrestors
- Ex i isolation amplifier
- Isolating relay
Gas analyzers
Suitability-tested field analyzers of Series 6 must be used to measure gases in hazardous areas.
The Series 6 analyzers are approved in accordance with Ex type of protection "Pressurized enclosure EEx p" for Zone 1 and Zone 2. In addition, these analyzers must be connected to monitoring equipment which must also be suitability-tested.
Exception: a pressurized enclosure is not required in zone 2 for the measurement of gases whose composition always remains below the lower explosive limit (LEL); in this case, it is sufficient for the field housing to be gas fume-proof (type of protection EEx n R).
Following pre-purging of 5 minutes, the monitoring equipment ensures that no gas fumes can enter the enclosure, and accumulation of the sample gas in the enclosure is prevented. The volume flow during the pre-purging phase is > 50 l/min. The protective gas is usually fed into the analyzer enclosure from a supply network via the monitoring equipment.
Category ATEX II 2G (Ex zone 1)
Two versions of pressurized enclosure EEx p complying with the directive 94/9/EC are available for use in zone 1:
-
Pressurized enclosure with compensation of losses resulting from leaks
The principle of this type of protection is based on prevention of ingress of the surrounding atmosphere or of the sample gas into the enclosure of the electrical equipment. Only that volume of protective gas is fed into the enclosure that is required to maintain an overpressure of at least 50 Pa compared to the sample gas pressure and atmospheric pressure. The maximum purging gas pressure is 165 hPa; this results in a maximum permissible sample gas pressure of 164 hPa; If the sample gas is combustible or occasionally flammable, the analyzer enclosure must be additionally purged with inert gas (e.g. nitrogen). In these cases, you must additionally ensure that the internal enclosure pressure is at least 5 mbar higher than the fail-safe-regulated sample gas pressure. If the pressure control of the sample gas is not fail-safe (= "double fault safety"), but only operationally safe (="single fault safety"), a differential pressure switch of the EEx p safety equipment must be used to signal if the sample gas pressure exceeds the purging gas pressure. This measure trips a safety shutdown. With occasionally flammable sample gas mixtures, flame arrestors must be additionally mounted externally at the sample gas inlet and outlet. Both the differential pressure switch and the flame arrestors come into contact with the sample gas and must therefore be made of corrosion-proof material, if applicable. Test certification: PTB 00 ATEX 2022 X Device identification: II 2 G Eex p [ia] ia IIC T4
-
Pressurized enclosure with continuous purging
The principle of this type of protection is based on having continuous purging of the Eex p enclosure after the pre-purge. It prevents ingress of the surrounding atmosphere and ensures that, for example, sample gas released through leaks is thinned to the extent that a combustible mixture cannot be created. The volume flow of the protective gas is fixed at 1 l/min and exceeds the maximum release volume by a factor of more than 100. Protective gas flows continuously through the enclosure with a volume flow of at least 1 l/min; in addition, the flow ensures that the enclosure pressure is increased to at least 50 Pa higher than the surrounding pressure. The max. permissible purging gas pressure is 25 hPa. The max. permissible sample gas pressure is equivalent to the permissible analyzer sample gas pressure. Test certification TUV 01 ATEX 1708 X Device identification: II 2 G EEx p [ia] ia IIC T4.
The fundamental safety requirements of both versions are satisfied by compliance with the European standards EN 50014:1997, EN 50016:1995, EN 50020:1994 and EN 954:1996.
The purging gas is monitored using EEx p monitoring equipment: This is a stand-alone unit which is connected electrically and pneumatically to the analyzer. Explosion protection is only provided when both devices are combined (analyzer and purging unit, and possibly further measures) (see below).
Category ATEX II 3G (Ex zone 2)
The principle of the type of protection "Pressurized enclosure for devices of Category 3" is based on preventing the ingress of any hazardous atmosphere into the gas analyzer.
Two versions complying with Directive 94/9/EC are available for use in Zone 2. In both cases, the standard devices of Series 6 (field version, not Ex) can be used.
-
Explosion protection due to gas-fumes-proof enclosure
The enclosure of the Series 6 gas analyzers (standard, field version) is sealed sufficiently to prevent gas fumes from penetrating. With this type of protection, only sample gases may be fed in which are below the LEL. Test certificate: TUV 01 ATEX 1686 X Device identification: II 3 G EEx n R II T6 It is not necessary to install a purging unit here.
-
Pressurized enclosure with continuous purging
Protective gas continuously flows through the enclosure with a volume flow of at least 1 l/min; furthermore, the flow results in an overpressure in the enclosure of at least 50 Pa compared to atmospheric pressure. The max. permissible purging gas pressure is 25 hPa. The max. permissible sample gas pressure is equivalent to the permissible analyzer sample gas pressure. Test certification TUV 01 ATEX 1697 X Device identification: II 2/3 G EEx n P II T4 The purging gas is monitored using E Ex p monitoring equipment. This is a stand-alone unit which is connected electrically and pneumatically to the analyzer. Explosion protection is only provided when these two units (analyzer and purging unit) are combined. (see below, purging unit)
The fundamental safety requirements of both versions are satisfied by compliance with the European standards EN 50014:1997, EN 50016:1995, EN 50020:1994 and EN 954:1996.
The EEx p monitoring equipment is a stand-alone unit which is connected electrically and pneumatically to the analyzer. Explosion protection is only provided when these two units are combined.
Category ATEX II 3D (Ex zone 22)
Ex zone 22 concerns the so-called dust protection. This is the European successor to the previous German zone 11. Zone 22 concerns the area in which during normal operation it is not expected that potentially explosive atmospheres occur in the form of a cloud of flammable dust in the air. Should such a cloud occur, however, then only briefly.
Considering the more stringent conditions for zone assignment, it can be expected that there will be increased demand for dust-protected analyzers.
The field versions of CALOMAT 6, OXYMAT 6 and ULTRAMAT 6 can be used in this zone according to the conformity statement TUV 03 ATEX 2278 X.
They are assigned the Ex identification II 3 D IP65 T60 °C or T65 °C or T85 °C or T135 °C.
However, this only concerns the so-called external explosion protection. With respect to the measurement of flammable gases, the additional measures applicable to gas explosion protection apply in addition, such as flame inhibitors. These separate certificates apply here.
FM/CSA Class I Div 2
The field versions of the standard analysis units can be used. Explosion protection is only provided when combined with the suitable equipment.
Definitions
Non-flammable gas
|
Gas or gas compositions with concentrations below the lower explosion limit (LEL). Non-explosive, even in contact with air. Example: CH4 < 4.4%; H2 < 4%; C2H2 < 2.3%
|
Flammable gas
|
Gas or gas composition with concentrations above the LEL. Explosive, but additionally requires air and ignition energy.
Example: CH4 > 4.4%; H2 > 4%; C2H2 > 2.3%
|
Explosive gas
|
Mixture of flammable gas and a gas matrix containing oxygen; between the LEL and the UEL (upper explosion limit). Already contains O2 and is explosive without additional air.
Example: 4,4 % ... 16.5% CH4 in air
Note: Very little data is available on the existing LEL and UEL for oxygen concentrations other than ambient air (20.95% O2) or for sample pressures other than atmospheric pressure.
|
Although the IEC and EN directives IEC 60079-10, EN 60079-10 (gas) and IEC 61241-10, EN 50281 (dust) do not specifically define the terms seldom, occasional, frequent, and permanent, the following interpretation is customary:
- Frequent or permanent: > 1 000 hours per year
> a frequent explosive atmosphere corresponds to Zone 0 or Class I, Div. 1
- Occasional: 10 to 1 000 hours per year
> an occasional explosive atmosphere corresponds to Zone 1 or Class I, Div. 1
- Seldom: < 10 hours per year
> a seldom explosive atmosphere corresponds to Zone 2 or Class I, Div. 2
The following additional safety mechanisms are recommended for continuous gas analyzers for measuring explosive gases (internal explosion protection). These requirements are based on the European ATEX approvals for analyzers, but can also be used as directives in the USA since no other specific definition exists there.
Categories of explosive gases
|
Analyzer model
|
ULTRAMAT 6 (ULTRAMAT 23)
|
OXYMAT 6
|
CALOMAT 6/62
|
Seldom explosive:
< 10 hours per year
|
None1)
|
None1)
|
None1)
|
Occasionally explosive:
10 … 1 000 hours per year
|
None1) 2)
|
Flame arrestors2)
|
Flame arrestors2)
|
Frequently or permanently explosive:
> 1 000 hours per year
|
Not permitted
|
Not permitted
|
Not permitted
|
Purging requirements
The continuous analyzers from Siemens with approvals for Class I, Div. 2 never require purging in a hazardous area in accordance with Class I, Div. 2 / Zone 2 under the aspect of area classification. All electronic and mechanical components are classified as “non-explosive” and can be used in environments in accordance with Class I, Div. 2 / Zone 2. However, purging may be necessary for a specific application, depending on the type of sample gas and the respective analyzer model in order to comply with the NEC and NFPA standards and to guarantee maximum possible safety as well as protection of the system.
NFPA 496 requirements for continuous gas analyzers and systems from Siemens
The NFPA 496 "Standard for Purged and Pressurized Enclosures for Electrical Equipment" describes in great detail and clarity the requirements for purging and for the pressurized enclosure for electric systems depending on 1) the external hazardous area classification, 2) the classification/grading of the system, 3) the type of gas in the gas path, and 4) the expected discharge of gas (none/limited/unlimited).
It is assumed for the internal gas path of a continuous gas analyzer that it exhibits only low losses under normal conditions and uncontrolled losses in the case of a mechanical failure (abnormal conditions).
When connecting gases with flammable components (> LEL) to the gas path of an analyzer with a hermetically sealed enclosure, the flammable component can become enriched in the inside of the analyzer enclosure – even under normal conditions – beyond a limit for continuous explosiveness and change the area classification (inside the analyzer enclosure) from "General Purpose" (Universal) or Class I, Div. 2 / Zone 2 to Class I, Div. 1 / Zone 0. This can also occur under abnormal conditions in any type of analyzer enclosure (including NEMA 1).
Analyzers for installation in the field – O6F, U6F and C6F – have a gas-tight enclosure (IP65 / NEMA 4 equivalent in accordance with IEC/EN 60529 and NEMA Standards Publication 250). Only a small natural exchange of air takes place with the environment. In accordance with NFPA 496, a limited discharge of gas is to be expected under normal conditions, and an unlimited discharge under abnormal conditions.
Analyzers for 19" rack mounting – O6E, U6E, U/O6, C6E, U23, O61, FID5 and FID6 – have an "open" enclosure (IP20 in accordance with IEC/EN 60529, no exact NEMA equivalent to IP20 available). A high natural exchange of air takes place with the environment unless the exchange is restricted. In accordance with NFPA 496, no discharge of gas is to be expected under normal conditions, but an unlimited discharge under abnormal conditions.
In the case of analyzers designed for general applications, it is assumed that they can ignite an explosive gas mixture at any time, and therefore no type of explosive atmosphere whatsoever may be present in the vicinity of these analyzers or within the enclosure at any time.
In the case of analyzers designed for Class I, Div. 2 / Zone 2 it is assumed that they cannot ignite an explosive gas mixture under normal conditions (single fault safety), and these analyzers can therefore be used in an occasionally explosive atmosphere in the environment or within the enclosure in accordance with the definition of Class I, Div. 2 / Zone 2. However, a frequent or permanent explosive atmosphere must be avoided since a simultaneous fault occurring on the electrical components of the analyzer could constitute an ignition source.
When purging a continuous gas analyzer or when purging/venting a continuous gas analyzer system suitable for Class I, Div. 2 / Zone 2 with instrument air or ambient air, and if failure of the safety vessel is not obvious, a leak detector (measurement in % of LEL) or similar equipment should be used in order to detect the unlimited discharge under abnormal conditions and to avoid a frequent or permanent explosive atmosphere inside the analyzer or in its environment. The leak detector must be fitted at a location where the escaping sample gas can be measured before becoming too greatly diluted. The alarm limit of the leak detector must be set to a level which enables detection of a dangerous state with consideration of the fact that the discharged sample gas has most probably already been diluted before it reaches the sensor.
Further important information
Gas paths material
It is strongly recommended that you use gas paths made of metal for applications with flammable gases since such gas paths offer the greatest safety. This particularly applies to analyzers or systems which are purged with instrument air or ambient air since an explosive atmosphere can be produced under abnormal conditions. This immediate danger does not exist in the case of analyzers or systems purged with inert gas.
It should be mentioned that, with an integrated system, all parts containing flammable gas (pumps, gas coolers, filters etc.) must be assessed in the same manner.
Purging of left-hand analyzer side (electronics side) of continuous gas analyzers for field installation
Since the left electronics side and the right measurement side of continuous gas analyzers are separated gas-tight from each other, it is unnecessary to purge the electronics side in most cases – purging of the (right-hand) measurement side is sufficient.
However, if doubt exists that flammable gas could penetrate the left-hand electronics side and become enriched there, it is advisable to purge both sides.
Further reasons for purging analyzers
- Corrosive sample gases: Purging with air or inert gas is necessary to prevent the enrichment of corrosive gas inside the analyzer, whereby operators or servicing personnel could be injured or the analyzer unit could be damaged. The discharged purging gas should be released at a non-critical point (collective vent etc.)
- Toxic gases: Purging with air or inert gas is necessary to prevent the enrichment of toxic gas inside the analyzer, whereby operators or servicing personnel could be injured. The discharged purging gas should be released at a non-critical point (collective vent etc.). Further information can be found in the OSHA directives for handling toxic materials.
Purging rate / applied pressure
Purging with air: The air throughput for purging an analyzer for field installation must be sufficient such that the concentration of flammable gases is less than 25% of the LEL (see NFPA 496, Section 8.3). An air throughput of 1 l/min is recommended.
Purging with inert gas: The inert gas throughput for purging an analyzer for field installation must be sufficient such that the oxygen level is less than 5% of the volume or, at a maximum, less than 50% of the oxygen required to form an explosive mixture (see NFPA 496, Section 8.3). An inert gas throughput of 1 l/min is recommended.
Applied pressure with inert gas: The purging and holding pressure applied to an analyzer for field installation must be sufficient such that the oxygen level is less than 5% of the volume or, at a maximum, less than 50% of the oxygen required to form an explosive mixture (see NFPA 496, Section 8.3). A pressure of 25 Pa (0.1 inch water column) in accordance with NFPA 496 is recommended. It should be taken into consideration when applying a pressure to an analyzer, that instead of continuous purging, flammable gas can collect within the analyzer if the sample gas pressure is higher than the purging pressure. It is recommendable to appropriately adapt the purging pressure within the permissible pressure range of the field device enclosure.
Exceptions: Inert gas should not be used as the purging gas for certain applications. This particularly applies to safety-related measurements of oxygen (LEL proof) where the sample gas has a slight overpressure and the inert gas used for purging could dilute the sample under abnormal conditions. Such applications require individual assessment of the purging equipment required and the mode of operation.
Integrated systems and analyzer containers: Purging or the application of pressure to continuous gas analyzer systems must be designed such that the requirements of NFPA 496 are complied with.
Leak detector
When purging a continuous gas analyzer or when purging/venting a continuous gas analyzer system suitable for Class I, Div. 2 / Zone 2 with instrument air or ambient air, and if failure of the safety vessel is not obvious, a leak detector (measurement in % of LEL) or similar equipment should be used in order to detect unlimited discharges under abnormal conditions and to avoid a frequent or permanent explosive atmosphere inside the analyzer or in its environment. The leak detector must be fitted at a location where the escaping sample gas can be measured before becoming too greatly diluted. The alarm limit of the leak detector must be set to a level which enables detection of a dangerous state with consideration of the fact that the discharged sample gas has most probably already been diluted before it reaches the sensor.
|
Deprecated: Function eregi() is deprecated in /home/h101150-2/siemens71.ru/docs/kip/kip.php on line 23
Deprecated: Function eregi() is deprecated in /home/h101150-2/siemens71.ru/docs/kip/kip.php on line 23
Deprecated: Function eregi() is deprecated in /home/h101150-2/siemens71.ru/docs/kip/kip.php on line 30
Deprecated: Function eregi() is deprecated in /home/h101150-2/siemens71.ru/docs/kip/kip.php on line 30
Deprecated: Function eregi() is deprecated in /home/h101150-2/siemens71.ru/docs/kip/kip.php on line 30
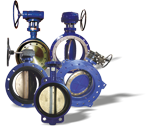
Deprecated: Function eregi() is deprecated in /home/h101150-2/siemens71.ru/docs/kip/kip.php on line 30
Deprecated: Function eregi() is deprecated in /home/h101150-2/siemens71.ru/docs/kip/kip.php on line 30
Арматура DENDOR
Deprecated: Function eregi() is deprecated in /home/h101150-2/siemens71.ru/docs/kip/kip.php on line 23
Deprecated: Function eregi() is deprecated in /home/h101150-2/siemens71.ru/docs/kip/kip.php on line 30
Deprecated: Function eregi() is deprecated in /home/h101150-2/siemens71.ru/docs/kip/kip.php on line 30
Deprecated: Function eregi() is deprecated in /home/h101150-2/siemens71.ru/docs/kip/kip.php on line 30
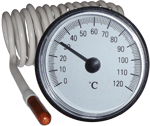
Deprecated: Function eregi() is deprecated in /home/h101150-2/siemens71.ru/docs/kip/kip.php on line 30
Deprecated: Function eregi() is deprecated in /home/h101150-2/siemens71.ru/docs/kip/kip.php on line 30
Датчики и измерители
Deprecated: Function eregi() is deprecated in /home/h101150-2/siemens71.ru/docs/kip/kip.php on line 23
Deprecated: Function eregi() is deprecated in /home/h101150-2/siemens71.ru/docs/kip/kip.php on line 30
Deprecated: Function eregi() is deprecated in /home/h101150-2/siemens71.ru/docs/kip/kip.php on line 30
Deprecated: Function eregi() is deprecated in /home/h101150-2/siemens71.ru/docs/kip/kip.php on line 30
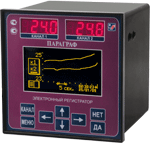
Deprecated: Function eregi() is deprecated in /home/h101150-2/siemens71.ru/docs/kip/kip.php on line 30
Deprecated: Function eregi() is deprecated in /home/h101150-2/siemens71.ru/docs/kip/kip.php on line 30
Регуляторы и регистраторы
Deprecated: Function eregi() is deprecated in /home/h101150-2/siemens71.ru/docs/kip/kip.php on line 23
Deprecated: Function eregi() is deprecated in /home/h101150-2/siemens71.ru/docs/kip/kip.php on line 30
Deprecated: Function eregi() is deprecated in /home/h101150-2/siemens71.ru/docs/kip/kip.php on line 30
Deprecated: Function eregi() is deprecated in /home/h101150-2/siemens71.ru/docs/kip/kip.php on line 30
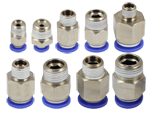
Deprecated: Function eregi() is deprecated in /home/h101150-2/siemens71.ru/docs/kip/kip.php on line 30
Deprecated: Function eregi() is deprecated in /home/h101150-2/siemens71.ru/docs/kip/kip.php on line 30
Пневматическое оборудование
Deprecated: Function eregi() is deprecated in /home/h101150-2/siemens71.ru/docs/kip/kip.php on line 23
Deprecated: Function eregi() is deprecated in /home/h101150-2/siemens71.ru/docs/kip/kip.php on line 30
Deprecated: Function eregi() is deprecated in /home/h101150-2/siemens71.ru/docs/kip/kip.php on line 30
Deprecated: Function eregi() is deprecated in /home/h101150-2/siemens71.ru/docs/kip/kip.php on line 30
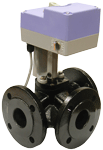
Deprecated: Function eregi() is deprecated in /home/h101150-2/siemens71.ru/docs/kip/kip.php on line 30
Deprecated: Function eregi() is deprecated in /home/h101150-2/siemens71.ru/docs/kip/kip.php on line 30
Краны и Клапаны
Deprecated: Function eregi() is deprecated in /home/h101150-2/siemens71.ru/docs/kip/kip.php on line 23
Deprecated: Function eregi() is deprecated in /home/h101150-2/siemens71.ru/docs/kip/kip.php on line 30
Deprecated: Function eregi() is deprecated in /home/h101150-2/siemens71.ru/docs/kip/kip.php on line 30
Deprecated: Function eregi() is deprecated in /home/h101150-2/siemens71.ru/docs/kip/kip.php on line 30
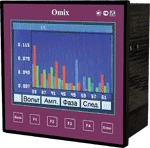
Deprecated: Function eregi() is deprecated in /home/h101150-2/siemens71.ru/docs/kip/kip.php on line 30
Deprecated: Function eregi() is deprecated in /home/h101150-2/siemens71.ru/docs/kip/kip.php on line 30
Измерительные приборы
Deprecated: Function eregi() is deprecated in /home/h101150-2/siemens71.ru/docs/kip/kip.php on line 23
Deprecated: Function eregi() is deprecated in /home/h101150-2/siemens71.ru/docs/kip/kip.php on line 30
Deprecated: Function eregi() is deprecated in /home/h101150-2/siemens71.ru/docs/kip/kip.php on line 30
Deprecated: Function eregi() is deprecated in /home/h101150-2/siemens71.ru/docs/kip/kip.php on line 30
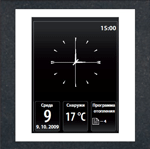
Deprecated: Function eregi() is deprecated in /home/h101150-2/siemens71.ru/docs/kip/kip.php on line 30
Deprecated: Function eregi() is deprecated in /home/h101150-2/siemens71.ru/docs/kip/kip.php on line 30
Системы беспроводного управления «умный дом»
Deprecated: Function eregi() is deprecated in /home/h101150-2/siemens71.ru/docs/kip/kip.php on line 23
Deprecated: Function eregi() is deprecated in /home/h101150-2/siemens71.ru/docs/kip/kip.php on line 30
Deprecated: Function eregi() is deprecated in /home/h101150-2/siemens71.ru/docs/kip/kip.php on line 30
Deprecated: Function eregi() is deprecated in /home/h101150-2/siemens71.ru/docs/kip/kip.php on line 30
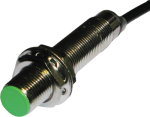
Deprecated: Function eregi() is deprecated in /home/h101150-2/siemens71.ru/docs/kip/kip.php on line 30
Deprecated: Function eregi() is deprecated in /home/h101150-2/siemens71.ru/docs/kip/kip.php on line 30
Бесконтактные выключатели Конечные выключатели Оптические датчики Энкодеры
Deprecated: Function eregi() is deprecated in /home/h101150-2/siemens71.ru/docs/kip/kip.php on line 23
Deprecated: Function eregi() is deprecated in /home/h101150-2/siemens71.ru/docs/kip/kip.php on line 30
Deprecated: Function eregi() is deprecated in /home/h101150-2/siemens71.ru/docs/kip/kip.php on line 30
Deprecated: Function eregi() is deprecated in /home/h101150-2/siemens71.ru/docs/kip/kip.php on line 30
Deprecated: Function eregi() is deprecated in /home/h101150-2/siemens71.ru/docs/kip/kip.php on line 30

Deprecated: Function eregi() is deprecated in /home/h101150-2/siemens71.ru/docs/kip/kip.php on line 30
SKW-FS - Установка умягчения
Deprecated: Function eregi() is deprecated in /home/h101150-2/siemens71.ru/docs/kip/kip.php on line 23
Deprecated: Function eregi() is deprecated in /home/h101150-2/siemens71.ru/docs/kip/kip.php on line 30
Deprecated: Function eregi() is deprecated in /home/h101150-2/siemens71.ru/docs/kip/kip.php on line 30
Deprecated: Function eregi() is deprecated in /home/h101150-2/siemens71.ru/docs/kip/kip.php on line 30
Deprecated: Function eregi() is deprecated in /home/h101150-2/siemens71.ru/docs/kip/kip.php on line 30
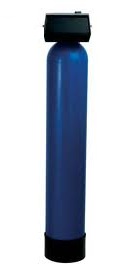
Deprecated: Function eregi() is deprecated in /home/h101150-2/siemens71.ru/docs/kip/kip.php on line 30
SKW-FK - Установка обезжелезивания
|